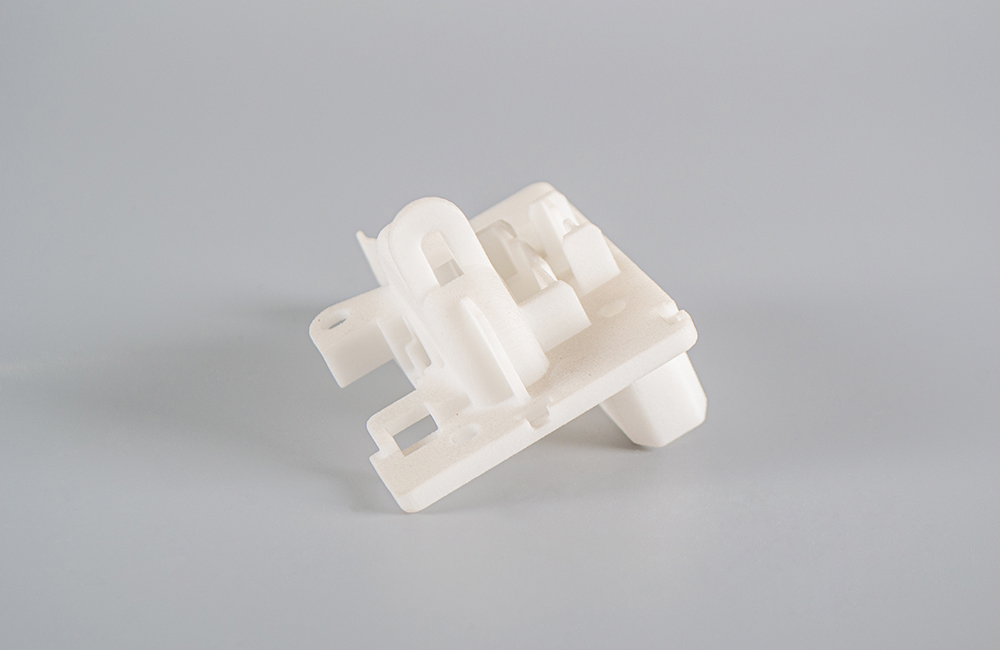
行业/分类:其他手板模型加工
加工方式: 3D打印 使用材料: 树脂
最小精度: 0.1mm 生产周期: 2~7天
产品尺寸: 5cm*5cm*4cm
后处理: 打磨
优点
缩短研发周期:传统制造手板模型的方式往往需要经过多道复杂工序,耗时较长。而 3D 打印技术能够直接根据设计模型快速制造出零件手板模型,大大减少了从设计到实物的时间,使通讯器材的研发进程加快,更快地推向市场。
降低成本:在产品开发初期,若采用传统制造方式制作模具来生产少量的手板模型,成本会很高。3D 打印无需制作复杂的模具,只需有数字模型文件即可进行打印,尤其对于小批量、复杂结构的通讯器材零件手板模型制作,成本优势明显。
高度定制化:通讯器材的更新换代快,对个性化和定制化的要求也越来越高。3D 打印技术可以根据不同的设计需求,轻松实现各种复杂形状和结构的零件手板模型制造,满足通讯器材多样化的设计要求,为产品创新提供了更大的空间。
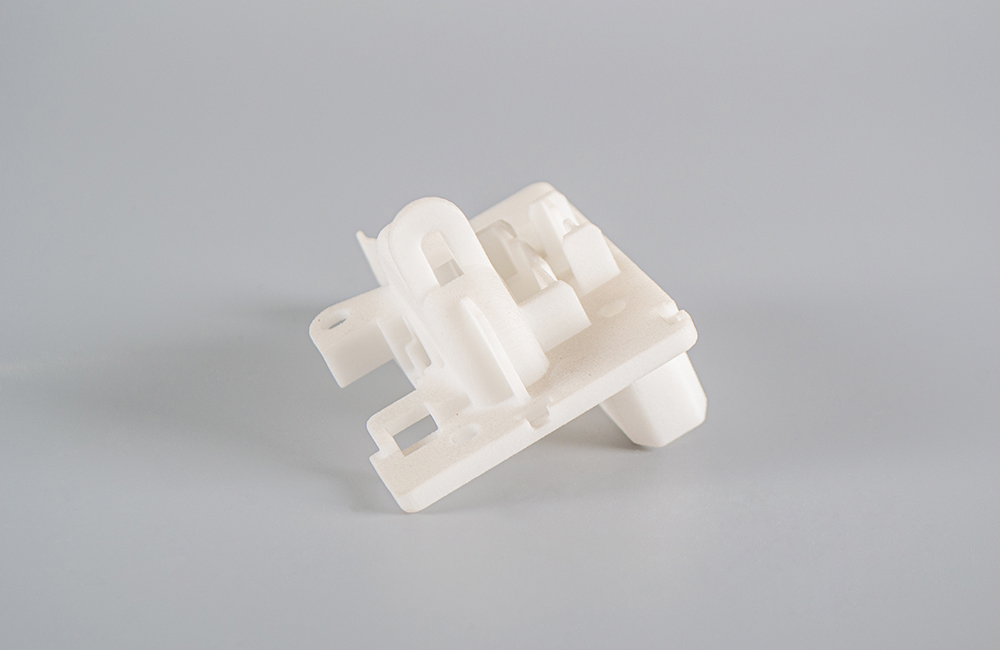
精度较高:目前的 3D 打印技术已经能够达到较高的精度,可以满足通讯器材零件手板模型对于尺寸精度和细节表现的要求,从而更准确地验证产品的设计和功能。
常用材料
光敏树脂:具有精度高、表面质量好的特点,能够打印出非常精细的结构和光滑的表面,适合制作对外观和细节要求较高的通讯器材零件手板模型,如手机外壳、按键等。
ABS 塑料:具有良好的机械性能和稳定性,强度较高,韧性较好,适用于制作一些需要承受一定外力或具有一定结构强度的通讯器材零件手板模型,如通讯设备的支架、外壳等。
尼龙:具有较高的强度和耐磨性,同时还具备一定的柔韧性,适合制作一些需要具备耐磨、耐腐蚀等特性的通讯器材零件手板模型,如连接器、插头等。
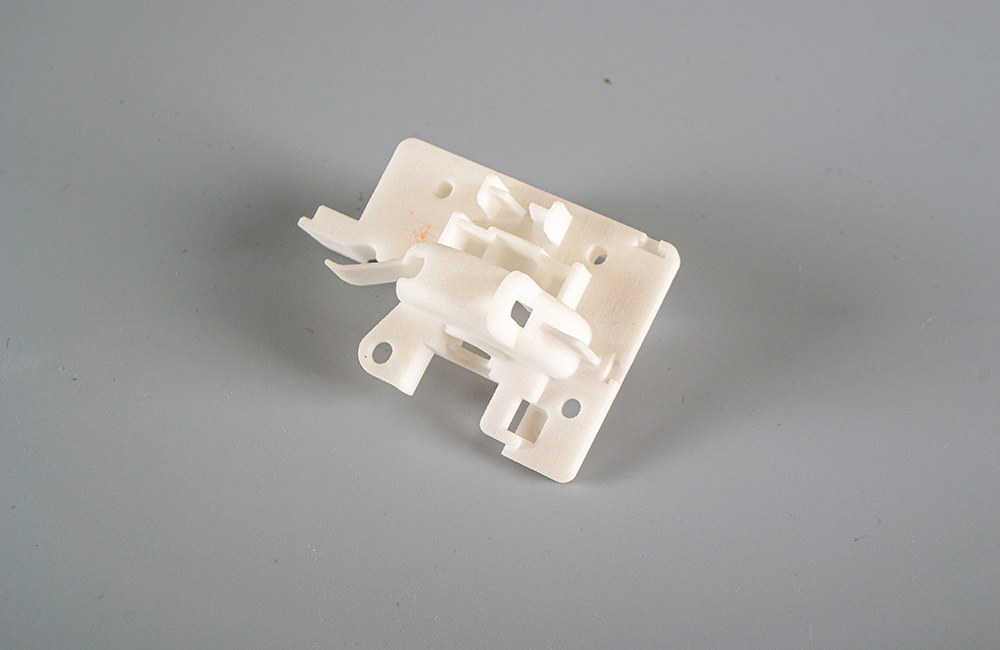
制作流程
3D 建模:设计师根据通讯器材零件的设计要求,使用专业的 3D 建模软件创建零件的三维模型。在建模过程中,需要考虑零件的尺寸、形状、结构、装配关系等因素,以确保模型的准确性和可制造性。
模型修复与优化:对创建好的 3D 模型进行检查和修复,确保模型没有错误和瑕疵。同时,根据 3D 打印的工艺特点和要求,对模型进行优化,如调整模型的壁厚、添加支撑结构等,以提高打印的成功率和质量。
选择 3D 打印设备和材料:根据通讯器材零件手板模型的具体要求,选择合适的 3D 打印设备和材料。不同的 3D 打印设备和材料具有不同的性能和特点,需要综合考虑零件的尺寸、精度、强度、外观等因素来进行选择。
3D 打印:将优化后的 3D 模型导入到选定的 3D 打印设备中,进行打印参数的设置,如打印层厚、打印速度、曝光时间等。设置好参数后,启动 3D 打印机进行打印,打印过程中需要注意观察打印情况,确保打印的顺利进行。
后处理:打印完成后,需要对零件手板模型进行后处理,包括去除支撑结构、打磨、抛光、喷漆、电镀等工艺,以提高模型的表面质量和外观效果,使其更接近最终产品的要求。
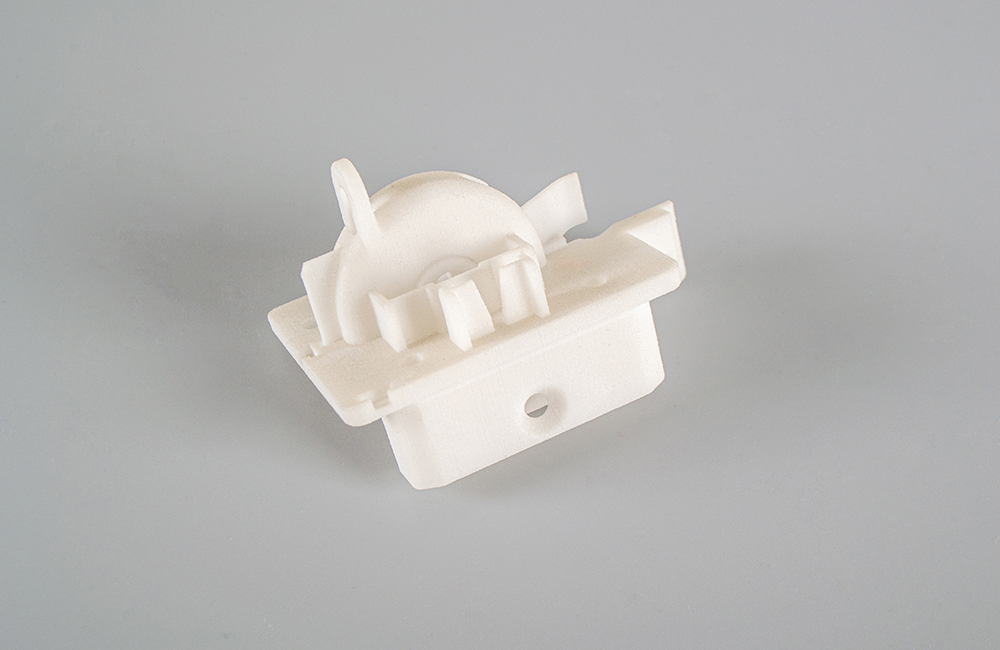
质量检测:对经过后处理的通讯器材零件手板模型进行质量检测,主要包括尺寸精度检测、外观检查、装配测试等。确保手板模型符合设计要求和质量标准,能够满足通讯器材的研发和测试需求。
应用案例
手机配件:如手机外壳、按键、摄像头模组、耳机插孔等零件的手板模型制作。通过 3D 打印技术,可以快速制造出不同设计方案的手机配件手板模型,进行外观和功能的验证,为手机产品的研发和改进提供依据。
基站设备:基站设备中的一些复杂结构零件,如滤波器、天线支架、散热器等,也可以采用 3D 打印技术制作手板模型。这些零件通常具有复杂的形状和结构,传统制造方式难度较大,而 3D 打印可以轻松实现其制造,帮助工程师更好地进行设计优化和性能测试 。
光通讯器件:光通讯器件对精度和表面质量要求较高,3D 打印技术可以制造出高精度的光通讯器件手板模型,如光纤连接器、光分路器等,用于光学性能测试和结构验证,提高光通讯产品的研发效率和质量 。