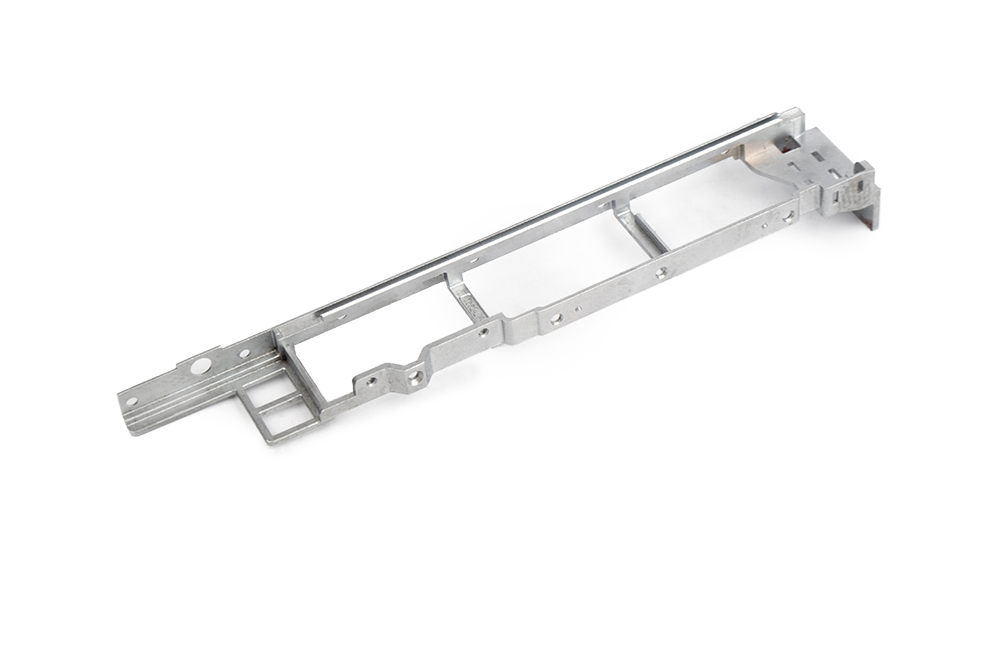
行业/分类:其他手板模型加工
加工方式: 压铸加工 使用材料: 铝合金
最小精度: 0.1mm 生产周期: 2~7天
产品尺寸: 30cm*5cm*2cm
后处理: 打磨
定义与作用
定义:压铸加工机械设备结构件手板是根据压铸加工机械设备结构件的设计图纸,通过一定的工艺方法制作出来的样品或模型,也被称为样件、验证件、样板等。
作用
检验设计:帮助工程师直观地检查结构件的设计是否合理,包括尺寸精度、装配关系、空间布局等方面,及时发现设计缺陷并进行优化,避免在正式生产模具制造后才发现问题,从而降低成本和缩短研发周期。
功能验证:对结构件的功能进行初步验证,如运动部件的灵活性、连接部位的可靠性等,确保结构件在实际使用中能够满足压铸加工机械设备的工作要求。
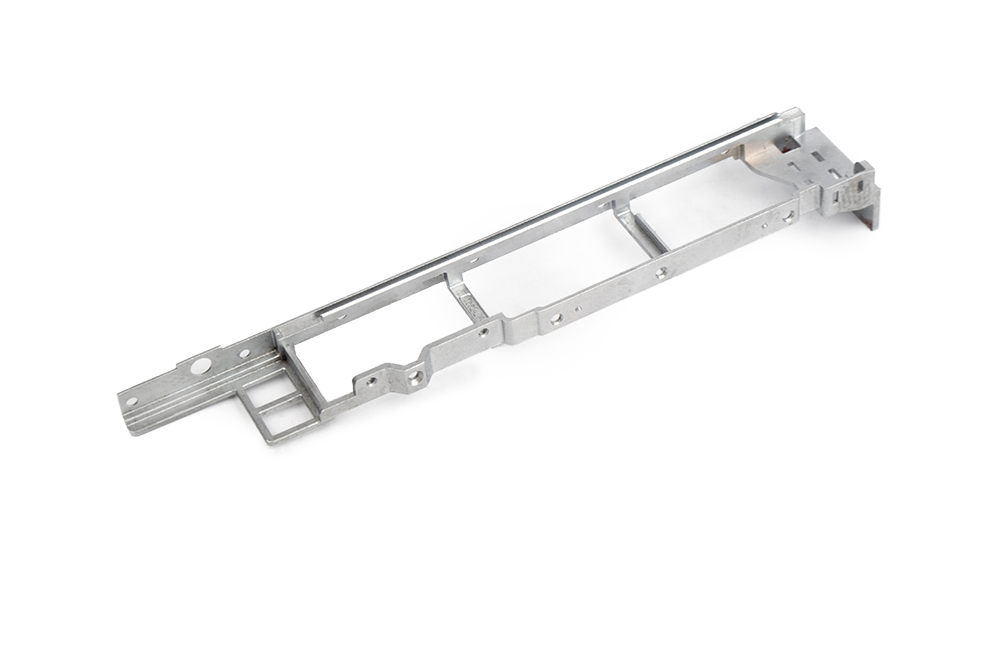
沟通交流:作为一种实物模型,方便设计团队、生产团队、客户以及其他相关人员之间进行沟通和交流,使各方对结构件的设计和性能有更清晰、准确的理解,有助于协调工作和达成共识。
制作材料
铝合金:具有密度小、强度高、耐腐蚀性好、导热性优良等特点,能够减轻设备重量,同时保证结构件的强度和刚性,适合制造各种压铸加工机械设备结构件手板,如外壳、支架、传动部件等。
锌合金:流动性好,易于压铸成型,能够获得高精度和复杂形状的结构件手板。而且锌合金的成本相对较低,在一些对成本较为敏感的场合应用较为广泛。
镁合金:具有比铝合金更高的比强度和比刚度,即相同重量下,镁合金结构件的强度和刚性更好,能进一步减轻设备重量,同时镁合金还具有良好的减震性能和电磁屏蔽性能,常用于制造一些对重量要求苛刻或有特殊性能要求的压铸加工机械设备结构件手板。
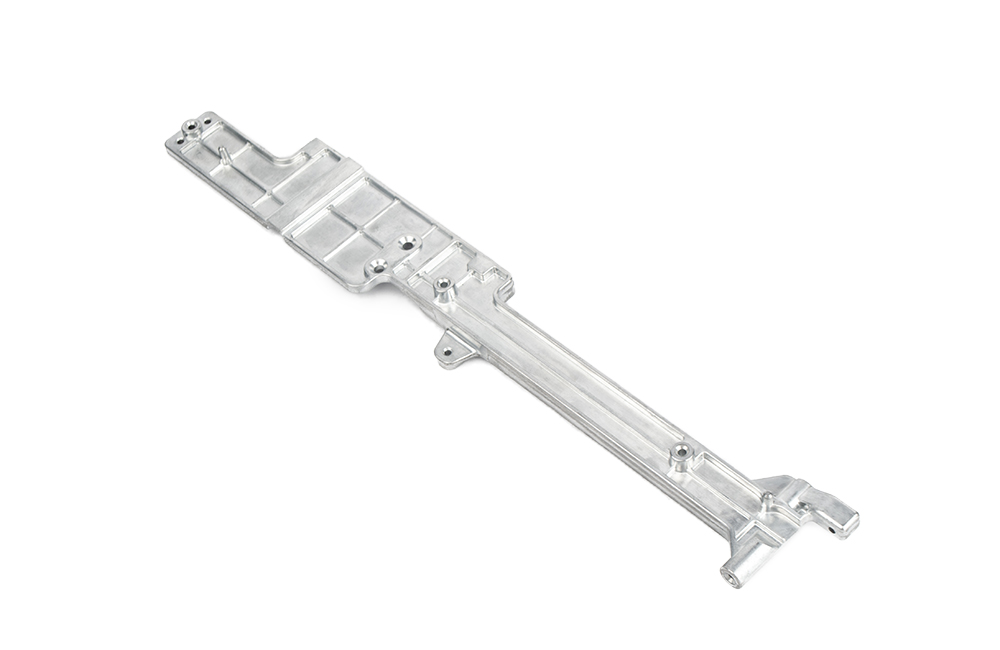
制作工艺
设计与模具准备
CAD 设计:使用先进的计算机辅助设计(CAD)软件,对压铸加工机械设备结构件进行精确的三维建模,确定结构件的形状、尺寸、公差等技术要求,为后续的模具制造和手板制作提供准确的设计数据。
模具制造:根据 CAD 设计模型,制造压铸模具。通常采用高强度合金钢材料,通过精密加工工艺,如数控铣削、电火花加工等,确保模具的精度和表面质量,以保证压铸出的结构件手板符合设计要求。
压铸过程
材料选择与熔炼:根据结构件手板的性能要求,选择合适的压铸合金材料,如铝合金、锌合金或镁合金等,并将所选合金材料在熔炉中加热至适宜的温度,使其熔化成液态,以备压铸使用。
模具预热:在压铸前,将模具预热至一定温度,以减少模具与液态金属之间的温差,避免因热应力导致模具开裂或变形,同时提高液态金属的流动性,有利于金属液在模具型腔中的填充。
高压注射:将熔化的金属液在高压作用下快速注入模具型腔中,使其在短时间内充满整个型腔,然后在压力下冷却凝固,形成所需的结构件手板形状。
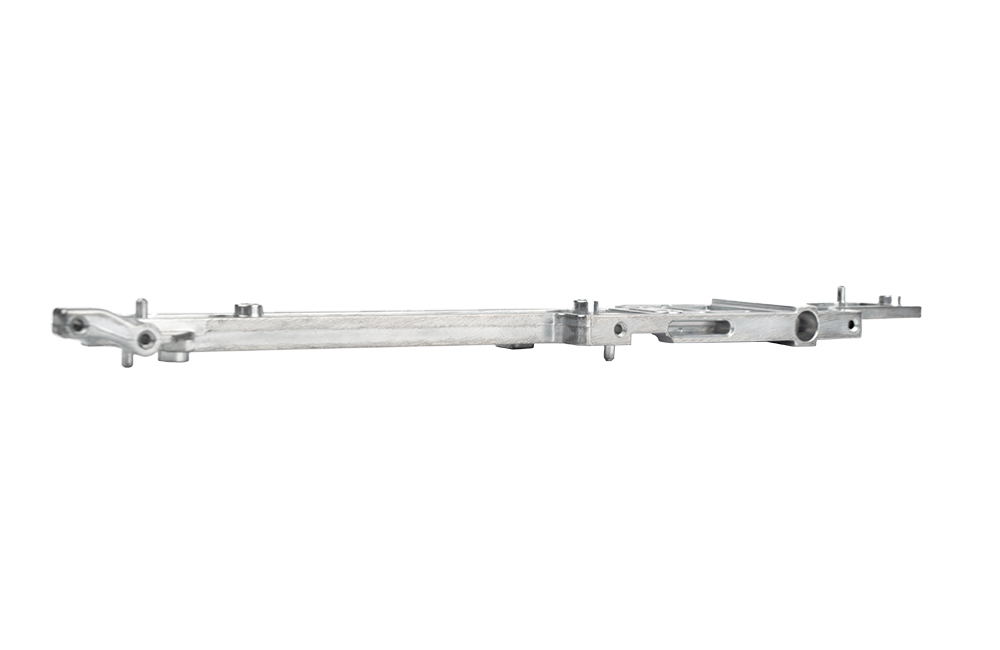
后处理
去毛刺:去除压铸件表面的毛刺、飞边和浇口等多余部分,使结构件手板的表面更加光滑,尺寸更加精确,提高外观质量和装配性能。
表面处理:根据产品的要求,对结构件手板进行各种表面处理工艺,如喷砂、抛光、电镀、阳极氧化等,以改善表面的光洁度、耐腐蚀性、耐磨性等性能,同时满足不同的外观需求。
质量检测
尺寸精度检测:使用精密测量仪器,如三坐标测量仪等,对结构件手板的关键尺寸进行测量,确保尺寸偏差在设计要求的公差范围内。
外观质量检查:目视检查结构件手板的表面质量,包括是否有气孔、砂眼、裂纹、缺料等缺陷,表面粗糙度是否符合要求,以及颜色、光泽度等是否均匀一致。
性能测试:根据结构件手板的实际使用要求,进行相应的性能测试,如硬度测试、强度测试、耐磨性测试、密封性测试等,以验证结构件手板是否满足压铸加工机械设备的性能要求。