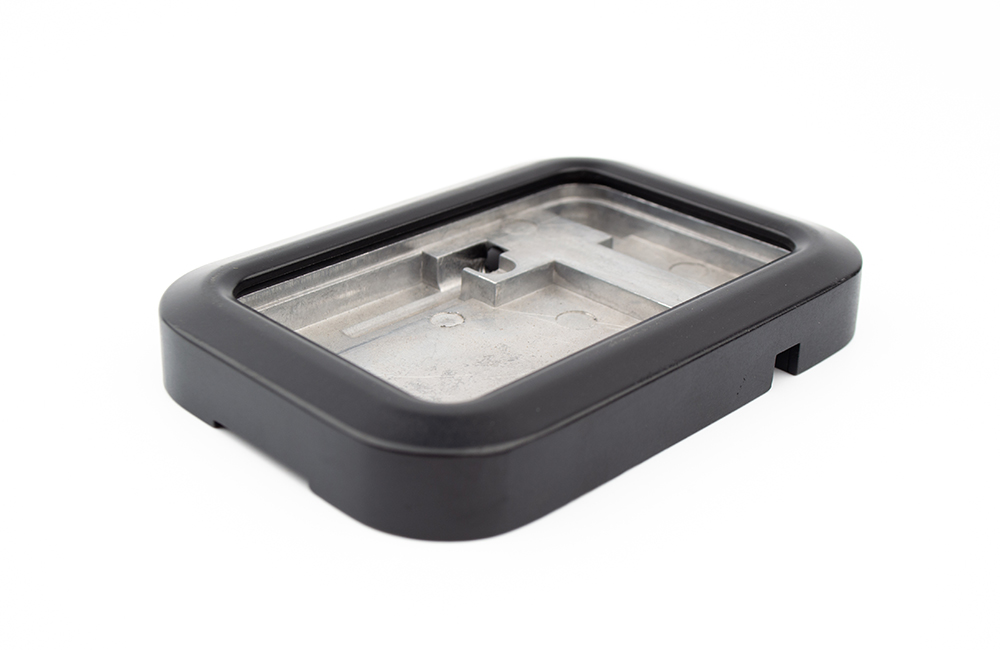
行业/分类:其他手板模型加工
加工方式: 压铸 使用材料: 铝合金
最小精度: 0.1mm 生产周期: 2~7天
产品尺寸: 18cm*8cm*2cm
后处理: 打磨,喷油
在压铸加工设备零件的手板模型制作过程中,需综合考虑材料选择、模具设计、工艺参数和后处理,以确保手板模型的精度、性能和成本效益。以下是关键注意事项:
1. 材料选择
- 适配压铸材料:
- 手板材料需与量产材料性能接近(如铝合金ADC12、锌合金ZA-8或镁合金AZ91D),以验证收缩率、流动性等特性。
- 若仅验证结构,可选用快速成型材料(如高精度树脂或3D打印金属粉末)。
- 成本与效率:
- 短期验证可用铝模(成本低、周期短),长期或高精度需求选择钢模(如H13模具钢)。
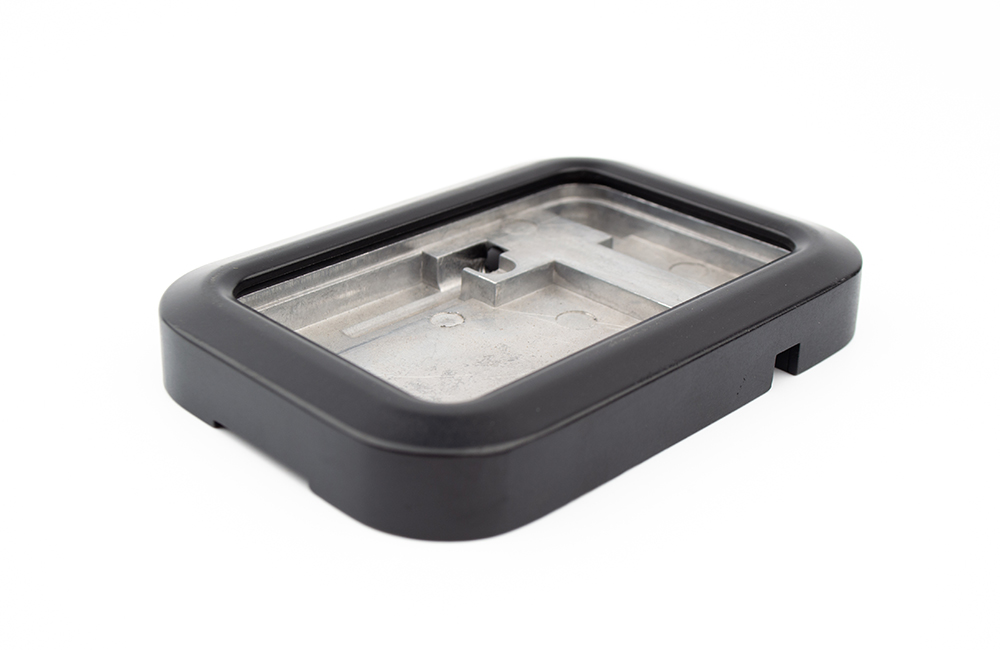
2. 模具设计要点
- 简化模具结构:
- 手板模具可省略复杂冷却系统,但需保留基本流道和浇口设计,验证填充效果。
- 分型面尽量简单,减少滑块和抽芯机构,降低成本。
- 缩尺补偿:
- 根据材料收缩率(铝合金约0.5%~0.7%,锌合金约0.3%~0.5%)调整模型尺寸。
- 排气与溢流:
- 设计排气槽(深度0.05~0.1mm)和溢流槽,避免气孔和填充不足。
3. 工艺参数优化
- 压铸参数设置:
- 注射压力:铝合金通常60~100MPa,锌合金20~50MPa,需根据零件壁厚调整。
- 模具温度:铝合金建议150~220°C,锌合金100~150°C,防止过早凝固。
- 压射速度:
- 薄壁件需高速填充(3~5m/s),厚壁件降低速度以减少湍流。
- 保压时间:
- 按壁厚计算(约1秒/mm),避免缩孔或变形。
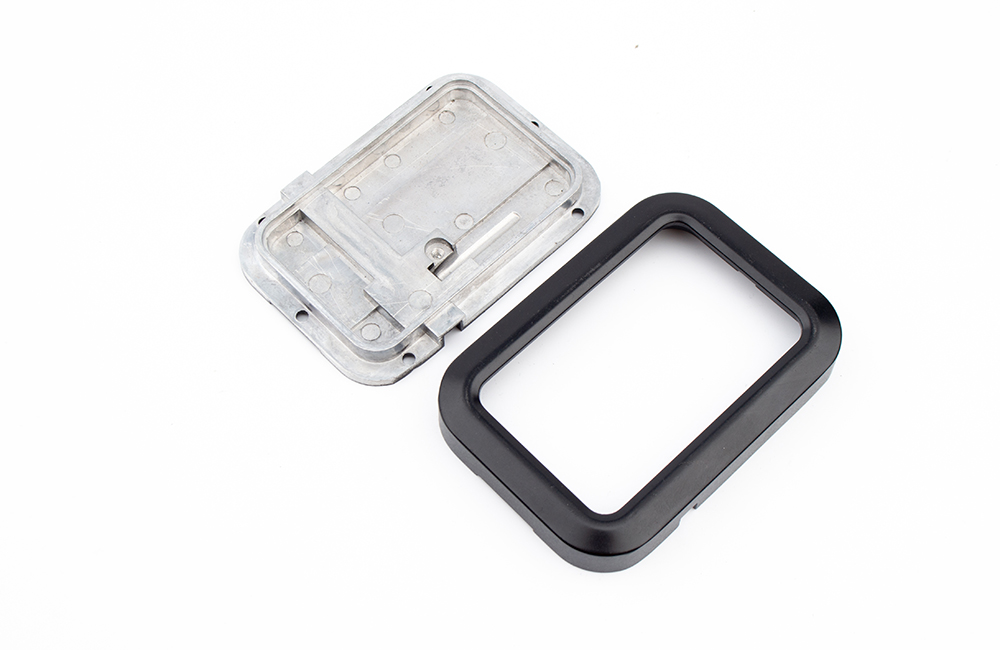
4. 后处理与检测
- 去毛刺与抛光:
- 手工或振动抛光去除分型线毛刺,关键配合面需CNC精加工。
- 表面处理:
- 喷涂底漆检查表面缺陷,或电镀/阳极氧化模拟量产效果。
- 尺寸检测:
- 使用三坐标测量仪(CMM)验证关键尺寸公差(通常±0.1mm)。
- 性能测试:
- 进行拉力、硬度测试(如铝合金HB60~100),验证力学性能。
5. 成本控制策略
- 快速模具技术:
- 使用3D打印砂模或硅胶模制作短期手板,降低开模成本。
- 模拟分析先行:
- 通过MAGMA或FLOW-3D软件模拟填充过程,减少试模次数。
- 小批量试产:
- 优先生产5~10件验证工艺稳定性,再优化模具细节。
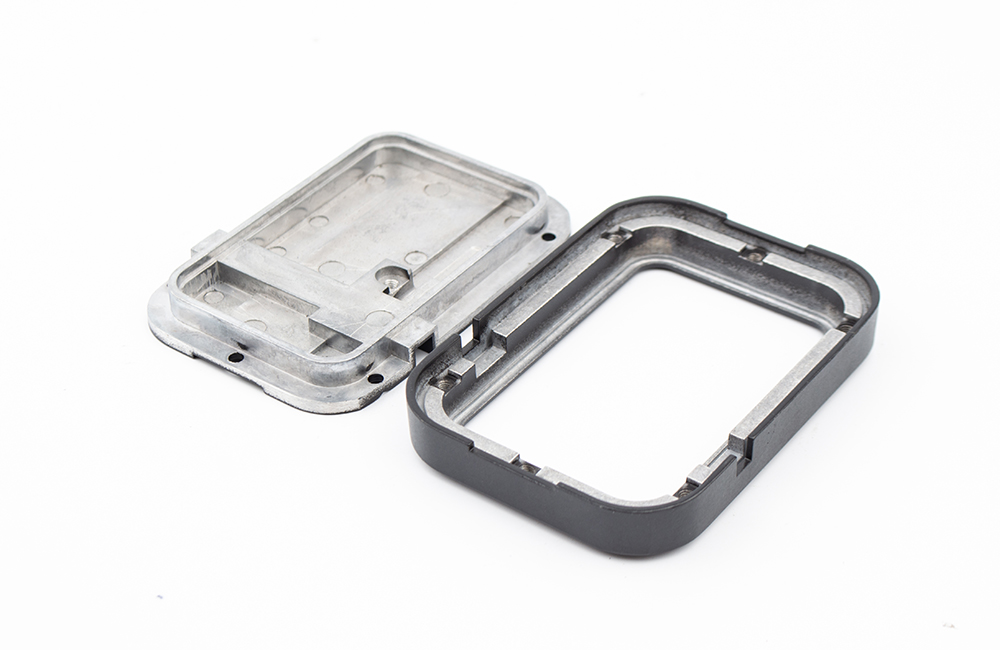
6. 常见问题与解决
- 气孔缺陷:
- 优化排气设计,降低注射速度,或采用真空压铸。
- 粘模问题:
- 模具表面镀钛处理或喷涂脱模剂(如水性蜡基)。
- 变形开裂:
- 调整保压时间,控制模具温度均匀性。
7. 手板应用场景
- 功能验证:测试装配干涉、运动机构合理性。
- 展示样品:用于客户确认外观或市场推广。
- 小批量试产:验证量产工艺可行性(50~500件)。
通过合理设计、精准工艺和严格检测,压铸手板模型可有效降低量产风险,缩短产品开发周期。若仅需快速验证,可结合3D打印(如SLM金属打印)与压铸工艺,平衡效率与成本。