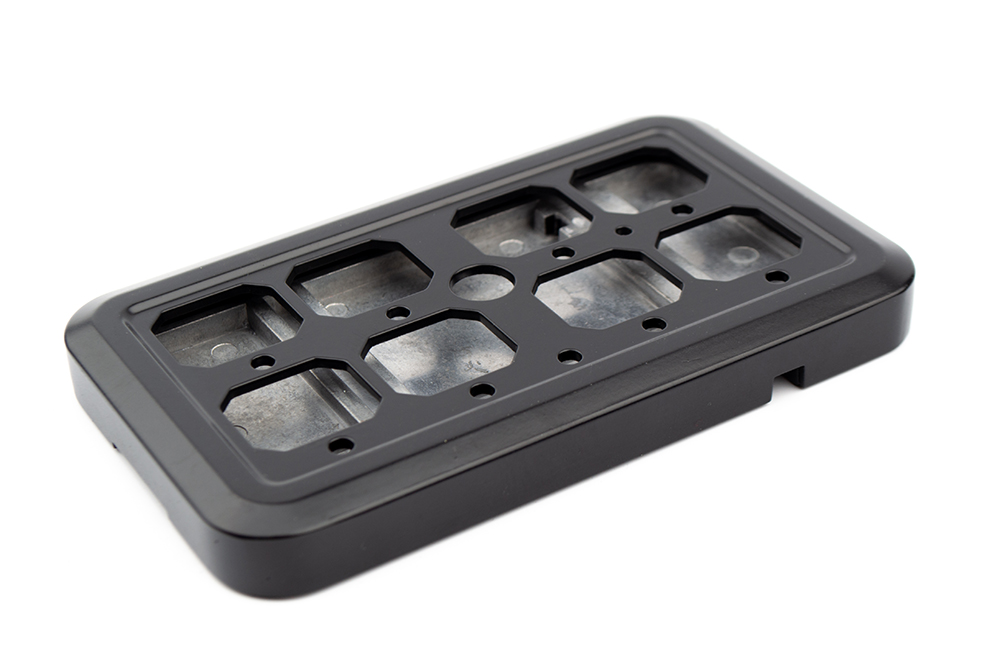
行业/分类:其他手板模型加工
加工方式: 压铸加工 使用材料: 铝合金
最小精度: 0.1mm 生产周期: 2~7天
产品尺寸: 18cm*8cm*2cm
后处理: 打磨
在压铸加工电源外壳手板模型时,需重点考虑电磁屏蔽性能、散热结构、模具设计合理性以及量产可行性。以下是关键步骤和注意事项:
1. 材料选择
- 核心需求:
- 电磁屏蔽:优先选择铝合金ADC12(流动性好、成本低)或镁合金AZ91D(轻量化、屏蔽性能更优)。
- 散热需求:若需高导热性,可选纯铝(如AlSi12,导热系数≈160 W/(m·K))。
- 耐腐蚀性:表面需阳极氧化或电镀处理(如镀镍)。
- 替代方案:
- 小批量验证可用锌合金ZA-8(易加工、表面光洁度高)。
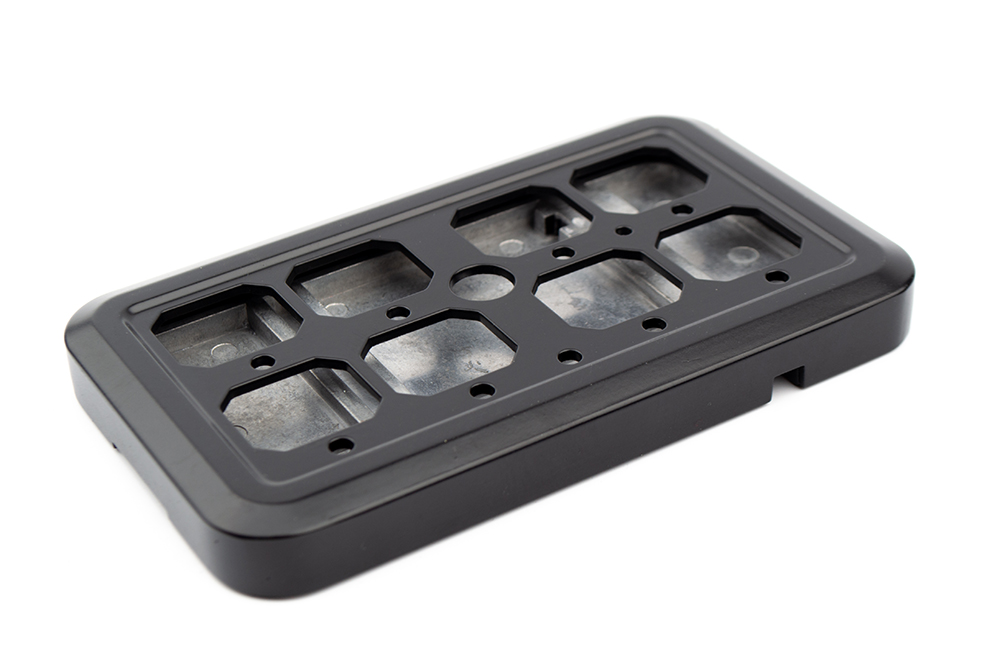
2. 模具设计要点
- 分型面设计:
- 分型线避开外观面(如Logo区域),隐藏于侧面或底部。
- 复杂内腔采用滑块结构,确保脱模顺利(如散热孔、接口凹槽)。
- 浇注系统优化:
- 浇口位置靠近壁厚区域(如安装柱),减少填充阻力。
- 流道截面采用梯形设计,降低湍流和卷气风险。
- 排气与溢流槽:
- 排气槽深度0.05~0.1mm,布局在金属液最后填充区域(如边角)。
- 溢流槽容量占零件体积5%~10%,用于容纳冷料和气体。
3. 压铸工艺参数
- 温度控制:
- 铝液温度:660~680°C(ADC12),模具预热温度150~200°C。
- 模温机分区控温,确保散热片区域快速冷却。
- 压力与速度:
- 注射压力:铝铸件60~100MPa,薄壁区域(<2mm)需高压高速填充。
- 压射速度:3~5m/s,避免金属液提前凝固。
- 保压与冷却:
- 保压时间≈壁厚×1.5(秒),如3mm壁厚保压4.5秒,减少缩孔。
- 冷却时间占总周期30%~50%,通过模温机精准控制。
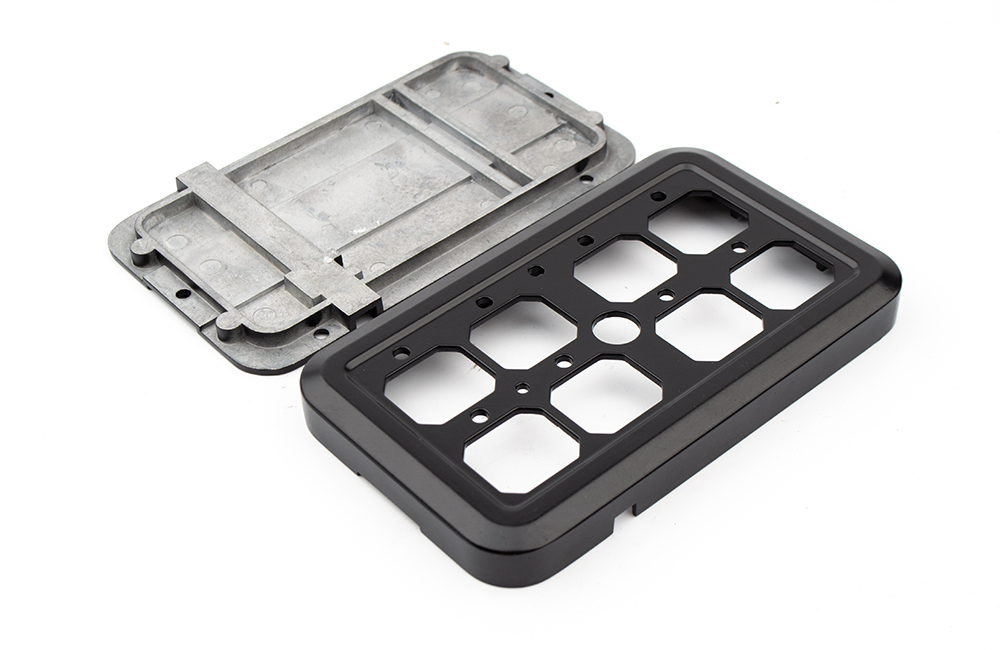
4. 结构设计关键点
- 壁厚均匀性:
- 主体壁厚2.5~3mm,局部加强筋厚度≥1.5mm(避免应力集中)。
- 散热片厚度1~1.5mm,间距≥2mm,高度≤15mm(防止填充不足)。
- 安装与密封结构:
- 螺丝柱根部加圆角(R≥0.5mm),预埋铜螺母(防松动)。
- 接缝处设计0.2~0.3mm密封槽,适配橡胶圈或硅胶垫。
- EMI屏蔽设计:
- 结合导电涂层(如镀层)或增加金属接触弹片结构。
5. 后处理与检测
- 去毛刺与整形:
- 重点处理分型线、散热孔边缘,使用振动抛光或CNC精修。
- 表面处理:
- 喷砂+阳极氧化:提升耐磨性和电磁屏蔽效果(如黑色硬质氧化)。
- 导电喷涂:内壁喷涂导电漆(表面电阻≤0.1Ω/sq)。
- 功能测试:
- 气密性:施加0.5~1MPa气压,检测泄漏率(≤0.1mL/min)。
- EMI测试:30MHz~1GHz频段内屏蔽效能≥60dB。
- 散热模拟:红外热像仪监测高功耗区域温升(对比设计值)。
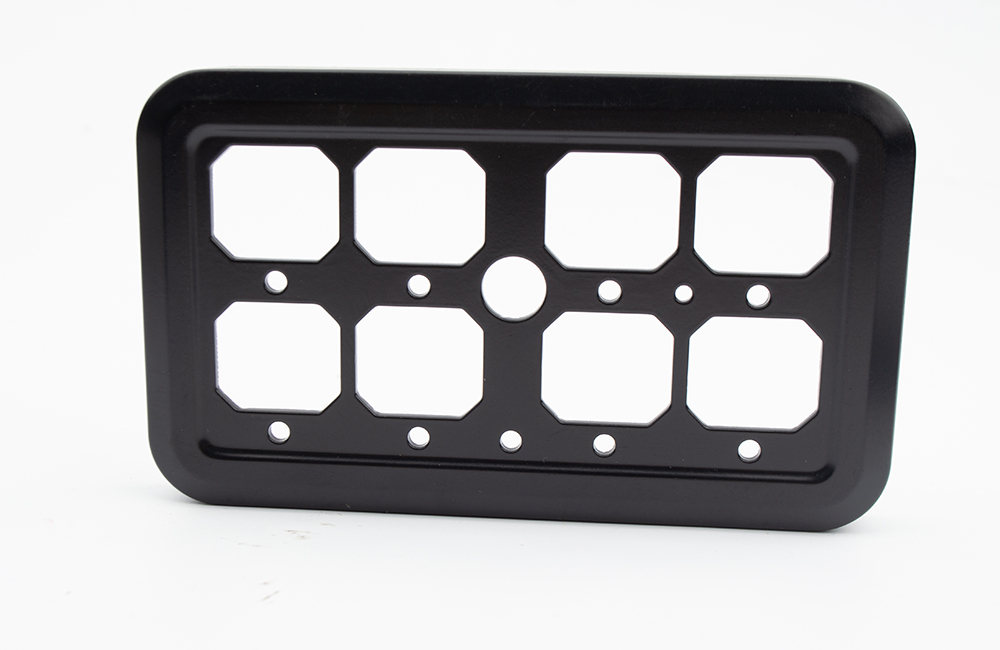
6. 成本控制策略
- 快速试模:
- 使用铝模(寿命≈5000次)替代钢模,降低初期成本。
- 3D打印砂芯验证复杂内腔结构(如散热风道)。
- 模拟分析:
- 通过MAGMA/ProCAST软件优化浇注系统,减少试模次数。
- 小批量验证:
- 首轮试产50~100件,重点检测尺寸稳定性和装配兼容性。
7. 常见问题与解决
- 气孔/缩孔:
- 优化排气设计,提高注射速度,或采用真空压铸。
- 局部加压:对厚壁区域延长保压时间。
- 变形翘曲:
- 增加加强筋或调整顶出位置(避免顶针力不均)。
- 时效处理:铝合金加热至150°C,保温2小时释放应力。
- 表面流痕:
- 提高模温至200°C以上,减少冷隔。
8. 手板应用场景
- 功能验证:测试散热效率、电磁兼容性(EMC)、防水等级(IP67)。
- 客户确认:提供带表面处理的全功能样品,用于订单确认。
- 小批量交付:替代传统开模周期,快速响应市场需求(500~1000件)。
9. 替代方案对比
方案 | 优势 | 劣势 |
---|---|---|
压铸铝合金手板 | 高精度、量产一致性 | 模具成本高(钢模≈¥10万~30万) |
CNC加工铝合金 | 免开模、快速迭代 | 成本高(单件≈压铸的3~5倍) |
3D打印(SLM铝) | 适合复杂内腔结构 | 表面粗糙、后处理耗时 |
通过合理设计、精准工艺和严格测试,压铸电源外壳手板模型可有效验证量产可行性。若时间紧迫,可结合CNC加工关键部位(如精密接口)与压铸主体结构,平衡效率与成本。