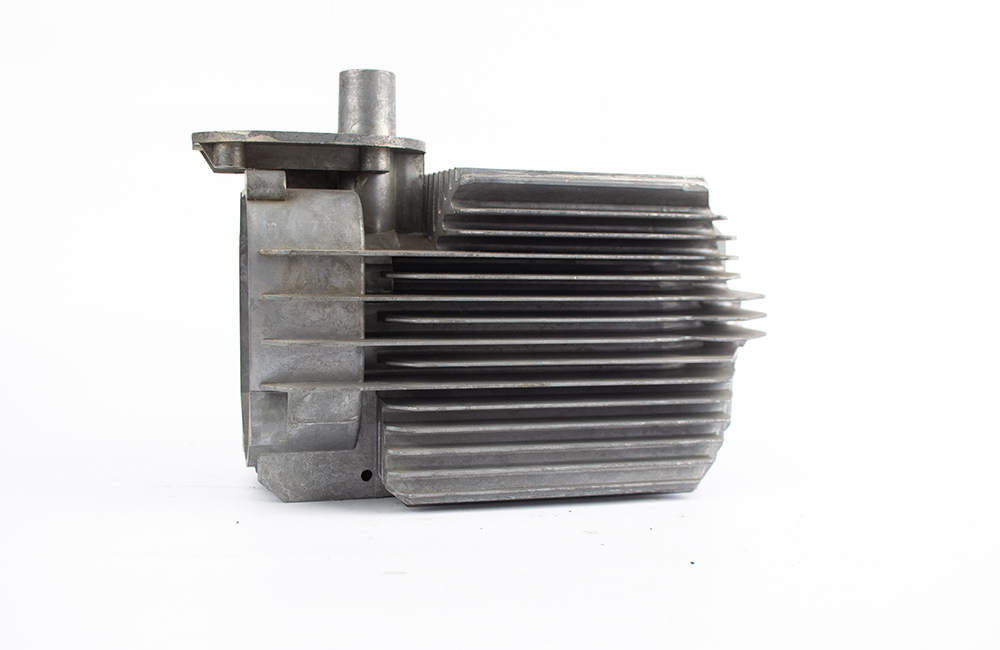
行业/分类:其他手板模型加工
加工方式: 压铸 使用材料: 铝合金
最小精度: 0.1mm 生产周期: 2~7天
产品尺寸: 25cm*15cm*15cm
后处理: 打磨
压铸加工是一种高效、精确的金属成型工艺,特别适用于生产复杂形状和精细结构的零件。当涉及到复杂散热器模型的压铸加工时,这个过程变得尤为关键,因为散热器往往具有复杂的几何形状和内部结构,以优化散热性能。以下是关于压铸加工复杂散热器模型的详细步骤和技术要点:
一、前期准备
模具设计与制造
设计考虑因素:根据散热器的使用要求、散热性能指标以及安装环境等,设计模具。对于复杂形状的散热器,如树枝状、针鳍状等,需要精准地规划模具的型腔布局,确保能够完整、清晰地复制散热器的细节特征。同时,要考虑材料的收缩率,保证压铸出来的散热器尺寸符合要求。
模具材料选择:选用适合压铸工艺的模具材料,如H13钢等热作模具钢。这种材料具有良好的热疲劳抗性、耐磨性和高温强度,能够承受压铸过程中的高温和高压,保证模具的使用寿命和压铸质量。
模具加工精度:利用高精度的加工设备,如高速铣床、电火花加工机床等,对模具进行加工。确保模具的型腔尺寸精度、表面粗糙度等达到设计要求,一般来说,型腔尺寸公差应控制在±0.05mm以内,表面粗糙度Ra不超过0.8μm,以保证散热器的表面质量和尺寸精度。
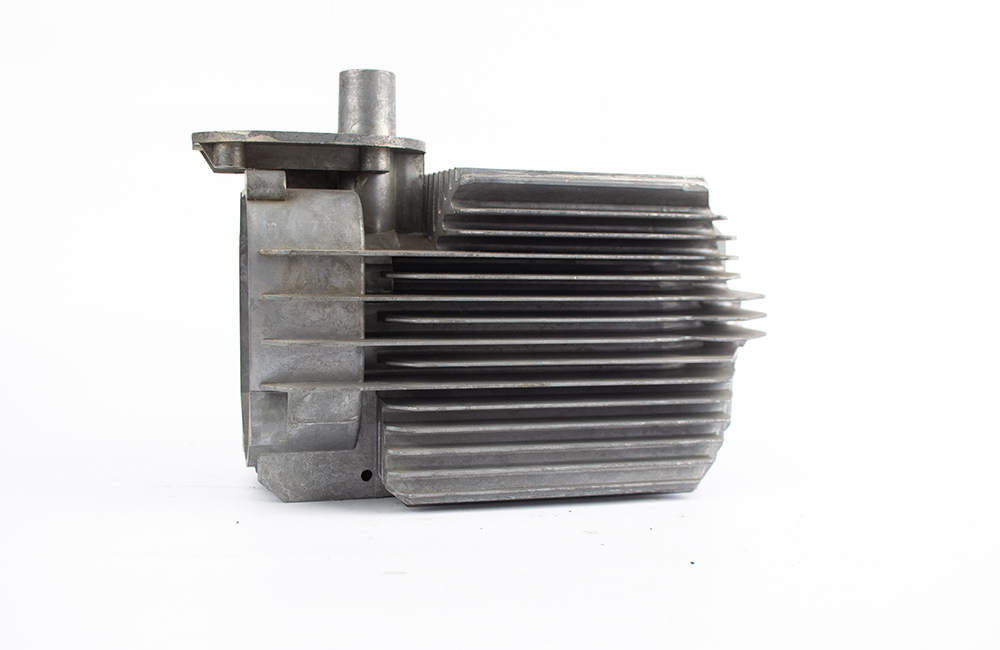
压铸材料选择
材料类型:常用的压铸材料有铝合金、锌合金等。铝合金具有良好的导热性、较轻的重量和较好的耐腐蚀性,适用于大多数散热器应用;锌合金则具有较低的熔点和较好的流动性,适用于制造形状复杂、薄壁结构的散热器。
材料质量控制:严格检查原材料的质量,包括材料的化学成分、纯度等。例如,铝合金中的主要合金元素含量应控制在标准范围内,杂质含量要低,以避免在压铸过程中产生气孔、夹渣等缺陷,影响散热器的性能和质量。
二、压铸过程
压铸机参数设置
压力控制:根据散热器的形状、尺寸和复杂度,合理设置压铸机的压射压力和增压压力。对于复杂形状的散热器,一般需要较高的压力来保证金属液能够充满模具的各个角落。通常,压射压力可设置在80 – 120MPa,增压压力可达到200 – 250MPa。
温度控制:精确控制压铸过程中的温度,包括压铸机压室温度、浇注温度和模具温度。铝合金的浇注温度一般在620 – 680℃,模具温度保持在200 – 250℃;锌合金的浇注温度约为420 – 480℃,模具温度在150 – 200℃。合适的温度有助于金属液的流动和填充,减少缺陷的产生。
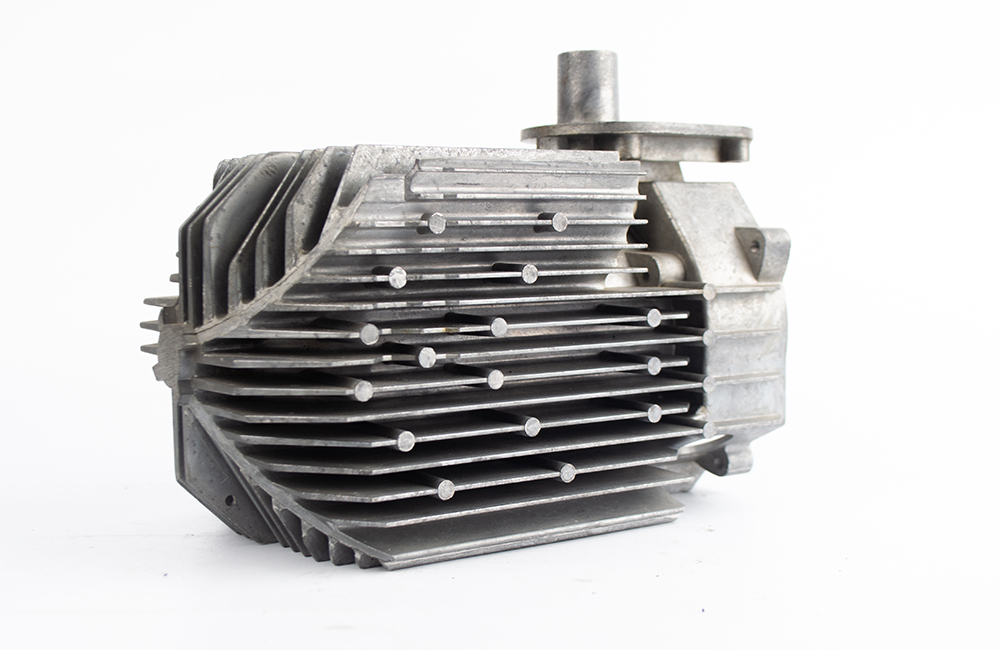
速度控制:调整压铸过程中的压射速度和充填速度。对于具有薄壁结构的散热器部分,应采用较快的压射速度,以确保金属液能够迅速填充型腔,避免产生冷隔、欠铸等缺陷。但在金属液接近充满型腔时,要适当降低速度,以减少卷气和溅沫的产生。
涂料使用
涂料选择:针对散热器的材料和模具材料,选择合适的压铸涂料。涂料应具有良好的润滑性、隔热性和耐金属液冲刷性。例如,对于铝合金散热器,可选用以石墨为主要成分的涂料,能够有效防止铝合金与模具之间的粘连,提高铸件的表面质量。
涂料涂抹方式:采用喷涂、刷涂等方式将涂料均匀地涂抹在模具型腔表面。注意涂料的厚度要适中,过厚可能会导致铸件表面出现缩痕、气泡等缺陷,过薄则起不到应有的作用。一般涂料厚度控制在0.1 – 0.2mm为宜。
三、后期处理
去毛刺和飞边处理
机械去毛刺:使用砂纸、锉刀等工具去除散热器表面的毛刺和飞边。对于一些难以用手工工具处理的部位,可采用振动研磨机或磁力研磨机进行处理,使散热器表面光滑平整。在去毛刺过程中,要注意避免损伤散热器的表面和结构。
化学去毛刺:对于一些复杂的内部通道或有精细结构的散热器,可采用化学去毛刺的方法。利用化学溶液的腐蚀性,将毛刺溶解去除。但要注意控制化学溶液的浓度、温度和处理时间,以免对散热器本体造成腐蚀。
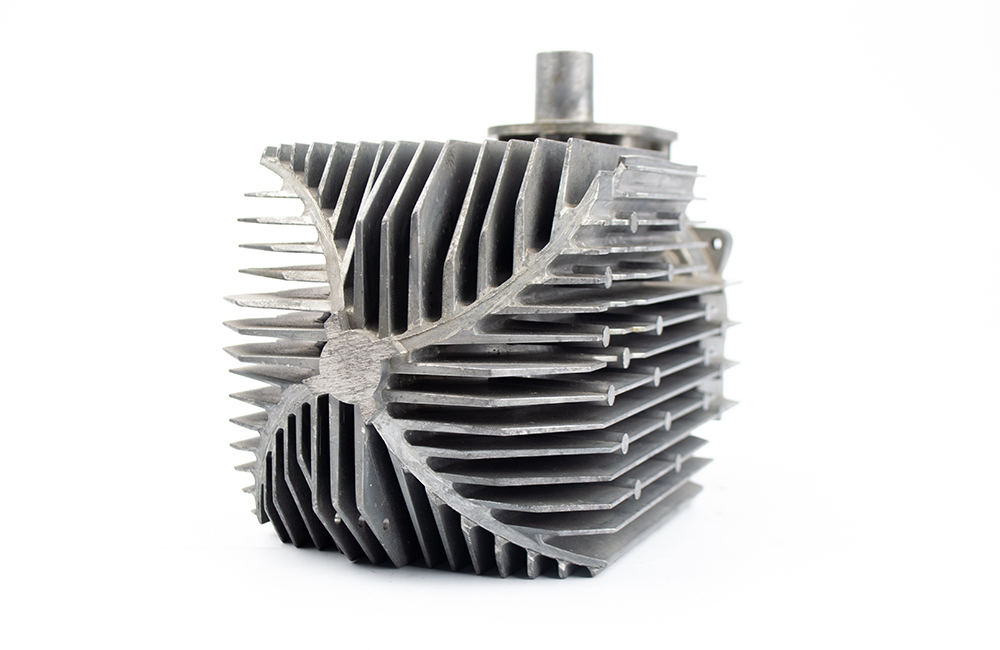
表面处理
清洗:在去毛刺后,要对散热器进行彻底清洗,去除表面的油污、残留的涂料、金属屑等杂质。可采用化学清洗剂进行清洗,然后用清水冲洗干净,确保散热器表面干净整洁。
涂装或阳极氧化处理:根据散热器的使用环境和外观要求,进行适当的表面处理。涂装可以提供良好的装饰效果和防护性能,如喷涂耐高温的绝缘漆等;阳极氧化处理则可以提高铝合金散热器的表面硬度、耐磨性和耐腐蚀性,氧化膜厚度可根据需要控制在5 – 20μm之间。
质量检测
尺寸检测:使用卡尺、千分尺、三坐标测量仪等量具对散热器的关键尺寸进行检测,确保其符合设计要求。对于具有复杂形状的散热器,要重点检测其安装尺寸、接口尺寸等部位的精度,尺寸公差一般应控制在设计尺寸的±0.2 – ±0.5mm范围内。
性能检测:对散热器进行散热性能测试,模拟实际的工作环境和散热条件,检测散热器的散热效率、热阻等参数是否符合设计指标。同时,还要进行压力测试、密封性测试等,确保散热器在使用过程中不会发生泄漏等问题。
通过以上步骤和技术要点的把控,可以实现复杂散热器模型的高质量压铸加工,满足各种应用场景的需求。