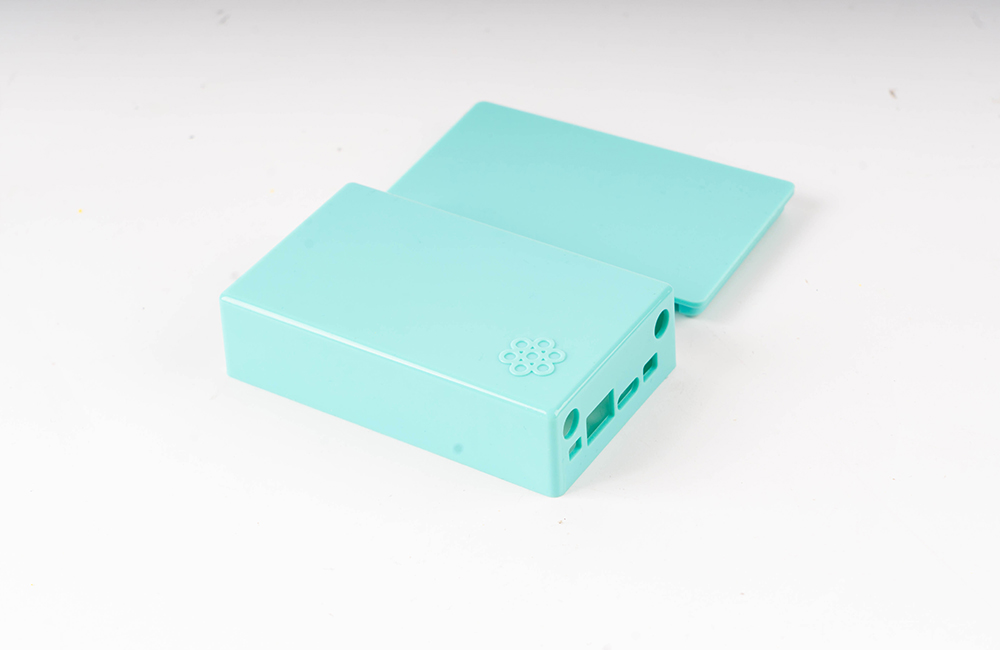
行业/分类:其他手板模型加工
加工方式: 注塑 使用材料: 塑料
最小精度: 0.1,mm 生产周期: 2~7天
产品尺寸: 15cm*10cm*5cm
后处理: 喷油
注塑加工电子设备外壳手板模型是一个将设计概念实体化、验证产品设计可行性以及测试功能的重要环节。以下是关于这一过程的详细解析:
一、注塑加工电子设备外壳手板模型的定义与目的
定义
注塑加工电子设备外壳手板模型是通过注塑工艺制作的电子设备外壳的样品。注塑工艺是一种将热塑性塑料或热固性塑料加热至熔融状态,然后注入模具型腔,经过冷却固化后得到与模具型腔形状一致的塑料制品的加工方法。
手板模型则是在新产品开发阶段,根据设计图纸制作出的实物模型,主要用于检验产品的外观、结构和功能等方面的可行性。
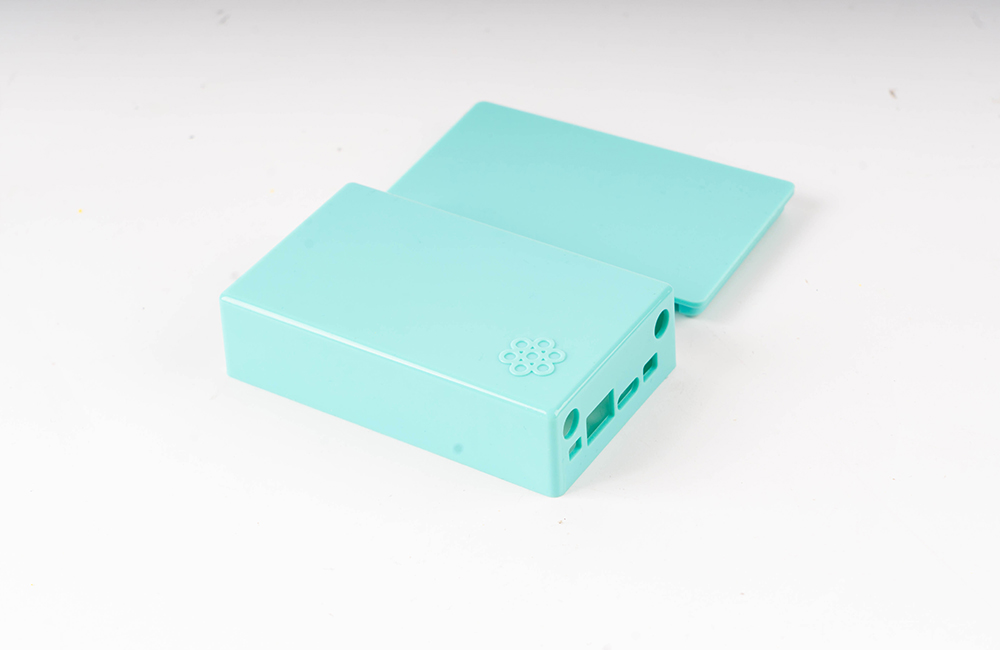
目的
验证外观设计:通过制作手板模型,可以直观地展示电子设备外壳的外观造型、颜色搭配和表面质感等,让设计师和客户能够实际感受产品的整体外观效果,及时发现并修改外观设计上的不足之处。
检验结构设计:检查外壳的手板模型的结构是否合理,包括卡扣、按键、接口、散热孔等部件的位置和尺寸是否合适,各部件之间的装配关系是否紧密,以及是否存在干涉现象等,确保产品在组装和使用过程中能够正常运行。
测试功能性能:对手板模型进行功能测试,如安装电子元件后的电路连通性、按键的灵敏度、接口的插拔性能等,验证产品是否满足设计要求和相关标准,避免因设计缺陷导致后期批量生产中出现的质量问题和售后问题。
评估生产工艺:模拟批量生产的注塑工艺参数,评估手板模型的成型质量,如是否有缩水、变形、翘曲等缺陷,为批量生产的工艺优化提供参考依据,提前发现并解决可能出现的生产工艺问题,降低生产成本和生产周期。
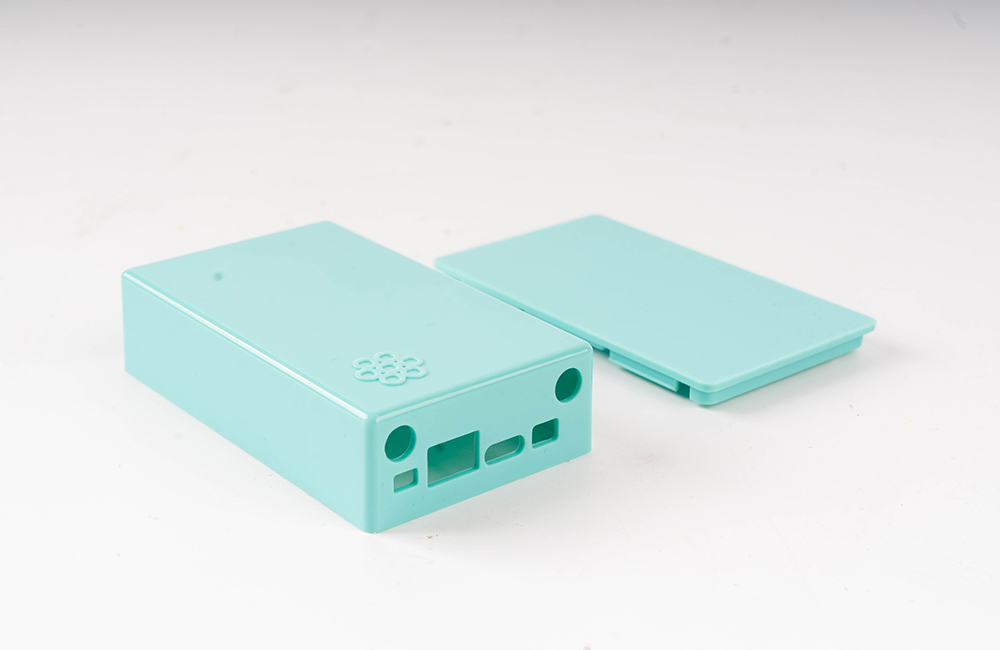
二、注塑加工电子设备外壳手板模型的制作流程
设计阶段
三维建模:设计师使用专业的三维设计软件,如SolidWorks、Pro/E、UG 等,根据电子设备的产品定位和设计要求,创建外壳的三维模型。在建模过程中,需要充分考虑产品的外观美感、人体工程学、结构强度和装配工艺等因素,确保设计的合理性和可行性。
模具设计:根据外壳的三维模型,设计注塑模具的结构。模具设计要考虑塑料的材料特性、收缩率、脱模方式、浇口位置和数量等因素,以确保能够顺利生产出高质量的手板模型。模具通常由动模和定模两部分组成,通过合理的设计和制造,保证在注塑过程中塑料能够均匀填充型腔,并在冷却后易于脱模。
编程与仿真:将设计好的三维模型转换为数控加工代码,并进行仿真分析。编程人员使用 Mastercam、PowerMILL 等编程软件,根据模具的结构和加工工艺要求,生成数控机床能够识别的 G 代码和 M 代码。通过仿真软件,如 Vericut 等,对编程代码进行验证和优化,检查刀具路径是否合理、是否存在碰撞干涉等问题,提高加工效率和质量,减少机床故障和刀具损坏的风险。
模具制作阶段
材料选择:根据模具的使用要求和成本预算,选择合适的模具材料,如钢材、铝合金、铜合金等。钢材具有较高的硬度和强度,适用于大规模生产的精密模具;铝合金则具有较轻的重量和良好的导热性能,适合制作小型、复杂形状的模具或快速原型制作;铜合金具有良好的导电性和导热性,常用于制作需要特殊散热性能的模具。
CNC 加工:利用数控机床按照编程代码对手板模型进行加工。CNC 加工可以保证较高的加工精度和表面质量,能够准确地加工出模具的各个部件,包括型腔、型芯、滑块、镶件等。在加工过程中,需要严格控制加工参数,如切削速度、进给量、切削深度等,以确保加工精度和表面粗糙度符合要求。
手工打磨与抛光:对 CNC 加工后的模具部件进行手工打磨和抛光处理,去除加工刀痕和毛刺,提高模具的表面光洁度和尺寸精度。手工打磨可以使用砂纸、锉刀、研磨膏等工具,从粗到精逐步进行打磨,使模具表面达到光滑平整的效果。抛光则可以进一步提高模具表面的光泽度和外观质量,常用的抛光方法有机械抛光、化学抛光、电抛光等。
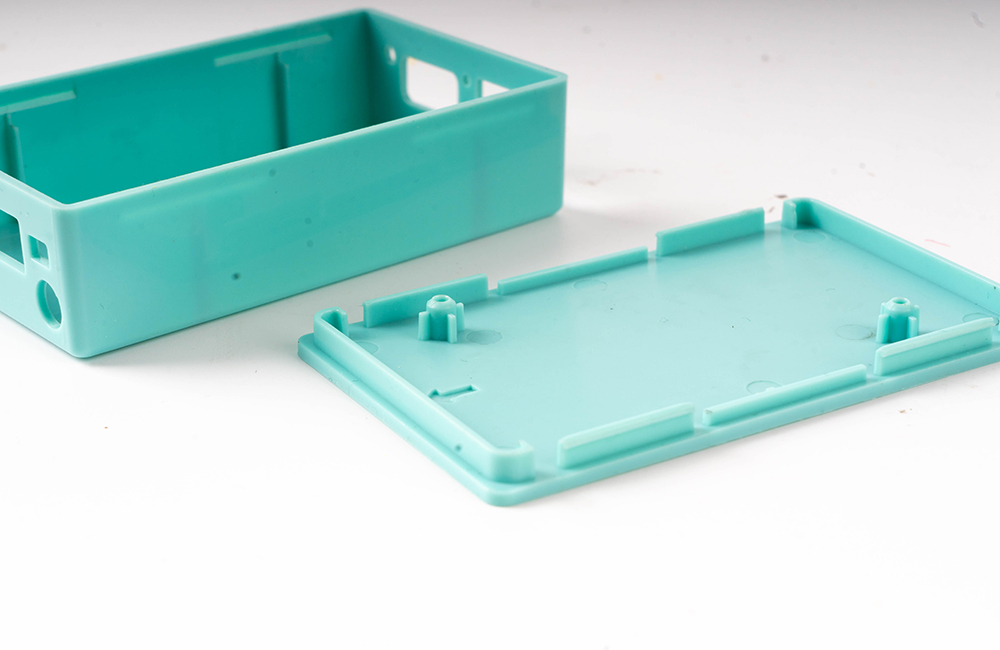
注塑成型阶段
材料准备:选择合适的塑料原料,如 ABS、PC、PMMA 等,并根据材料的干燥要求进行预处理。塑料原料在使用前需要进行干燥处理,以去除水分和挥发物,防止在注塑过程中产生气泡、银纹等缺陷。干燥的方式通常有自然干燥、烘箱干燥、真空干燥等,根据材料的性质和含水量选择合适的干燥方法和条件。
注塑参数设置:根据塑料材料的特性和手板模型的要求,设置注塑机的参数,如料筒温度、模具温度、注射压力、保压压力、注射时间、冷却时间等。这些参数的设置直接影响到手板模型的成型质量和外观效果,需要通过试验和调试来确定最佳的参数组合。一般来说,料筒温度应保证塑料能够充分熔化和均匀混合,模具温度应控制在一定范围内,以保证塑料的充模能力和冷却速度适中。
注塑成型:将干燥好的塑料原料加入注塑机的料筒中,经过加热熔化后,在注射装置的作用下,将熔融的塑料注入模具型腔中。塑料在型腔中冷却固化后,开模取出手板模型。在注塑过程中,需要注意观察产品的成型情况,及时调整注塑参数,避免出现缺料、烧焦、溢料等缺陷。
后处理阶段
修剪与打磨:对手板模型进行修剪和打磨处理,去除多余的飞边、毛刺和浇口痕迹,使产品的边缘光滑整齐。修剪可以使用剪刀、刀具等工具进行,打磨则可以使用砂纸、锉刀、研磨机等设备,根据产品的表面要求和精度要求选择合适的工具和方法进行打磨。
装配与测试:将经过后处理的手板模型进行装配,安装电子元件和其他配件,进行功能测试和外观检查。在装配过程中,需要确保各个部件之间的装配精度和连接强度,避免出现松动、卡滞等问题。功能测试包括电气性能测试、机械性能测试、环境适应性测试等,确保手板模型能够满足设计要求和使用标准。
表面处理:根据客户的需求和产品的设计要求,对手板模型进行表面处理,如喷漆、丝印、电镀、烫金等,以提高产品的外观效果和防护性能。表面处理可以使产品具有不同的颜色、光泽度和纹理效果,增强产品的美观度和辨识度。
综上所述,注塑加工电子设备外壳手板模型是一个集设计、加工、测试于一体的综合过程。通过这一过程,可以有效地验证产品设计的可行性,优化生产工艺,提高产品质量和市场竞争力。