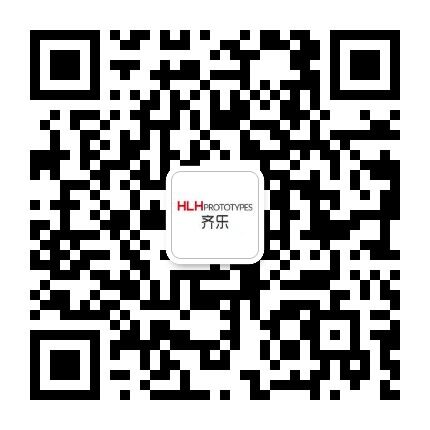
微信客服

在线客服
机加工做样品怎么做
发布时间:2025年03月26日
机加工做样品是一个涉及设计、材料选择、加工工艺和后处理等多个环节的过程。以下是详细的步骤和相关要点:
明确需求与功能
产品用途分析:深入了解样品的应用场景和功能要求。例如,如果是制作一个机械零件样品,需要考虑其在整机中的作用,如传动、支撑、密封等。根据用途确定样品的基本形状、尺寸范围和性能指标。
用户需求调研:与相关人员(如产品研发人员、客户代表等)沟通,获取对样品外观、手感、操作便利性等方面的特殊需求。比如,如果是一个手持工具样品,用户可能希望手柄部分符合人体工程学,握持舒适。
绘制设计图纸
二维绘图:使用专业的CAD(计算机辅助设计)软件,如AutoCAD,绘制样品的二维工程图。工程图应包括主视图、俯视图、左视图等多个视图,清晰地标注出各个部分的尺寸、公差范围、表面粗糙度等技术要求。例如,对于一个有孔的零件,要在图纸上精确标注孔的直径、位置度公差。
三维建模:利用SolidWorks、Pro/E等三维建模软件创建样品的三维模型。三维模型可以更直观地展示样品的形状和结构,便于进行虚拟装配和干涉检查。在建模过程中,要考虑实际加工的可能性,避免设计出无法通过机加工实现的结构。
根据设计要求选材
材料性能考虑:依据样品的功能和工作环境,选择合适的材料。例如,对于需要承受高应力的机械零件,可选用高强度合金钢;对于有耐腐蚀要求的样品,不锈钢或铜合金可能是较好的选择。同时,要考虑材料的硬度、韧性、耐磨性等性能指标。
工艺性评估:所选材料应具有良好的机加工性能。例如,铝材适合进行高速切削加工,易于铣削和车削,且表面质量容易控制;而一些难加工材料,如钛合金,虽然性能优异,但加工难度大,成本高,需要在加工设备和工艺上有更高的要求。
材料采购与检验
采购渠道选择:从可靠的供应商处采购材料,确保材料的质量符合要求。可以选择有良好信誉的材料生产厂家或经销商,查看其提供的材质证明、质量检测报告等文件。
材料检验:对采购回来的材料进行检验,包括外观检查(是否有裂纹、砂眼等缺陷)、尺寸测量(是否符合订购尺寸)、化学成分分析(对于一些特殊材料)等。例如,对于钢材,可以通过光谱分析检查其化学成分是否达标。
确定加工方法
车削加工:如果样品是回转体零件,如轴类、套类零件,可采用车削加工。在车床上,通过工件的旋转和刀具的移动,去除材料形成所需的形状。例如,制作一个简单的圆柱形零件,可以使用车刀进行外圆车削、端面车削等操作。
铣削加工:对于具有平面、槽、齿轮等结构的样品,铣削是一种常用的加工方法。利用铣床,通过铣刀的旋转和工件的移动,对材料进行切削。比如,加工一个带有矩形槽的平板零件,可以使用立铣刀进行铣槽操作。
钻削加工:当样品上有孔时,采用钻削加工。根据孔的直径和精度要求,选择合适的钻头和钻孔工艺。例如,对于精度要求较高的深孔,可能需要采用深孔钻削,并配合适当的冷却润滑措施。
磨削加工:用于提高样品表面的粗糙度和尺寸精度。特别是对于高精度的零件,磨削可以去除少量的材料,达到很高的表面质量。例如,经过淬火后的零件,通过磨削可以修正变形,获得良好的尺寸精度和表面粗糙度。
制定工艺路线
粗加工 – 半精加工 – 精加工路线:一般先进行粗加工,快速去除大部分余量,接近最终形状,但留有一定的加工余量。然后进行半精加工,进一步缩小加工余量,提高尺寸精度和表面质量。最后进行精加工,使样品达到设计要求的尺寸公差、表面粗糙度和其他技术要求。例如,对于一块板材零件,先通过铣削进行粗加工,去除大部分多余的材料,然后进行较精细的铣削作为半精加工,最后采用磨削完成精加工。
合理安排工序顺序:考虑各加工工序之间的相互影响和依赖关系。例如,对于一些需要热处理的零件,应在粗加工之后、精加工之前安排热处理工序,以消除加工应力,改善材料的切削性能。同时,要避免在后续工序中破坏已经完成的加工表面。
数控编程(针对数控机床)
程序编写:如果使用数控机床加工样品,需要根据设计图纸和工艺规划编写数控程序。对于简单的零件,可以手工编程;对于复杂的零件,通常使用CAM(计算机辅助制造)软件自动生成程序。例如,使用Mastercam软件,将三维模型导入后,设置刀具路径、切削参数等参数,生成数控程序代码。
程序验证:在实际加工前,通过软件模拟或在数控机床上进行空运行来验证程序的正确性。检查刀具路径是否合理,是否会与工件、夹具发生碰撞等。例如,在模拟过程中,观察刀具的运动轨迹是否符合预期,是否存在过切或欠切的情况。
机床设置与调试
刀具安装:根据加工工艺要求,选择合适的刀具并正确安装在机床上。例如,对于车削加工,要安装合适的车刀,调整好刀具的位置和角度;对于铣削加工,要安装铣刀并确保其紧固可靠。同时,要检查刀具的磨损情况,及时更换磨损严重的刀具。
工件装夹:选择合适的夹具将工件牢固地装夹在机床工作台上。夹具的选择要根据工件的形状和加工要求来确定。例如,对于圆柱形零件,可以使用三爪卡盘或顶尖等夹具;对于平板类零件,可以使用平口钳或螺栓压板等夹具。确保工件装夹稳定,不会在加工过程中发生位移或振动。
机床参数设置:设置机床的各种参数,如主轴转速、进给速度、切削深度等。这些参数要根据材料性质、刀具性能和加工要求来确定。例如,对于硬度较高的材料,主轴转速应适当降低,进给速度也应减小,以保证加工质量和刀具寿命。
样品加工
按程序加工:按照编写好的数控程序或工艺规程进行样品加工。在加工过程中,要密切关注机床的运行状态,如刀具的切削声音、工件的振动情况等。例如,如果发现刀具切削声音异常增大或工件振动明显,可能是刀具磨损或加工参数不合理,应立即停机检查。
过程记录:记录加工过程中的各项数据,如切削时间、刀具使用情况、加工中出现的问题及解决方法等。这些记录对于后续的质量分析和工艺改进具有重要意义。
质量控制
尺寸测量:在加工过程中,定期使用量具(如卡尺、千分尺、量表等)对样品的关键尺寸进行测量。例如,对于轴类零件,要测量其直径、长度等尺寸;对于有孔的零件,要测量孔的直径和位置度。将测量结果与设计图纸的要求进行对比,确保尺寸精度符合要求。
表面质量检查:检查样品的表面质量,包括表面粗糙度、有无划痕、裂纹等缺陷。可以使用粗糙度仪测量表面粗糙度,用目视或放大镜检查表面是否有划痕、裂纹等问题。对于表面质量不符合要求的部分,分析原因并采取相应的措施进行修复或返工。