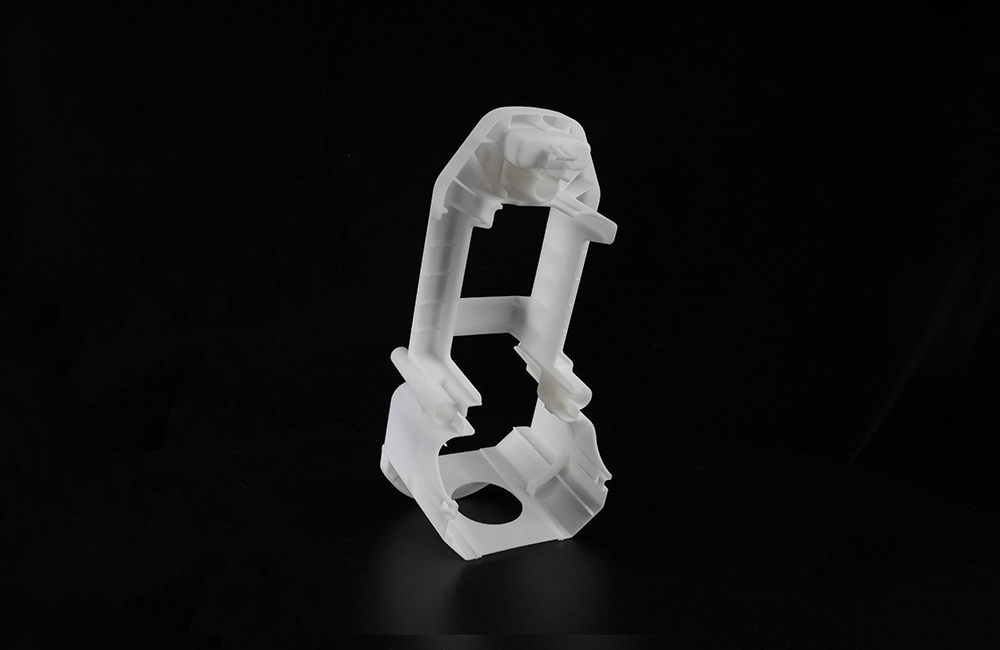
行业/分类:其他手板模型加工
加工方式: 3D打印 使用材料: 树脂
最小精度: 0.1mm 生产周期: 2~7天
产品尺寸: 15cm*5cm*3cm
后处理: 打磨
SLS(选择性激光烧结)是一种常用的增材制造技术,在打印汽车零件手板模型方面有以下特点和应用:
技术原理
SLS 技术使用高能量激光束扫描粉末材料床,如尼龙、聚苯乙烯等高分子粉末,或者金属粉末。激光束根据三维模型的切片数据,有选择地将粉末颗粒加热至熔点或烧结温度,使粉末颗粒相互粘结,形成一层固体截面。然后,工作台下降一个层厚的距离,重复上述过程,层层叠加,最终构建出三维的汽车零件手板模型。

优点
材料选择广泛:可以使用多种材料进行打印,包括尼龙、金属等,能满足不同汽车零件对手板模型材料性能的要求,如强度、韧性、耐高温性等。
高精度:能够实现较高的尺寸精度和表面质量,一般精度可达 ±0.1mm – ±0.2mm,可满足汽车零件手板模型对细节和尺寸准确性的严格要求。
复杂结构制造能力强:对于具有复杂内部结构、镂空设计或自由曲面的汽车零件,SLS 打印无需额外的支撑结构,能够直接制造出复杂形状的手板模型,有助于缩短产品研发周期和降低成本。
快速成型:从数字模型到实体手板模型的转化速度快,能够在较短时间内为汽车研发团队提供模型,便于进行设计验证、装配测试和性能评估等工作,加快产品开发进程。

缺点
设备成本高:SLS 打印机价格昂贵,通常在几十万元到数百万元不等,且维护成本也较高,这增加了汽车零件手板模型的制作成本。
材料成本较高:一些高性能的粉末材料价格相对较高,如某些金属粉末,导致手板模型的制作成本上升。
后处理复杂:打印完成后,手板模型需要进行后处理,如去除未烧结的粉末、表面打磨、抛光等。对于金属零件,还可能需要进行热处理、浸渗等后处理工艺,以提高零件的性能和质量,这增加了制作周期和工作量。

应用场景
外观验证:用于制作汽车外观件的手板模型,如车身外壳、保险杠、格栅等,帮助设计师直观地评估产品的外观设计效果,进行色彩、纹理和表面处理的测试,及时发现和修改设计缺陷。
装配验证:打印汽车内部结构件和零部件的手板模型,如发动机缸体、变速器壳体、仪表盘支架等,用于装配测试,检查零件之间的配合精度和干涉情况,优化产品的结构设计,提高装配效率和质量。
功能测试:可以制作具有一定力学性能和功能的汽车零件手板模型,如悬挂系统部件、转向系统零件等,进行初步的功能测试和性能评估,为后续的产品优化和工程设计提供参考依据。