
行业/分类:其他手板模型加工
加工方式: 注塑 使用材料: 塑料
最小精度: 0.1mm 生产周期: 2~7天
产品尺寸: 20cm*5cm*3cm
后处理: 喷油
流程
产品设计:根据遥控器的功能和外观需求,使用专业的设计软件进行三维模型设计,确定遥控器外壳的尺寸、形状、按键布局等细节。
手板制作:常见的手板制作方法有 CNC 加工、3D 打印和硅胶复模等。
模具设计与制造:依据手板模型和生产需求进行模具设计,确定模具的分型面、浇注系统、顶出机构等,然后使用数控机床等设备进行模具加工制造。

注塑成型:将经过干燥处理的塑料颗粒加入注塑机料筒,加热熔融后在一定压力和速度下注入模具型腔,冷却固化后得到遥控器外壳制品。
后处理:对注塑成型后的遥控器外壳进行去毛刺、飞边,表面抛光、喷涂、丝印等后处理操作,以提高外壳的外观质量和性能。
质量检测:采用外观检查、尺寸测量、性能测试等方法,对遥控器外壳进行全面检测,确保产品符合设计要求和质量标准。
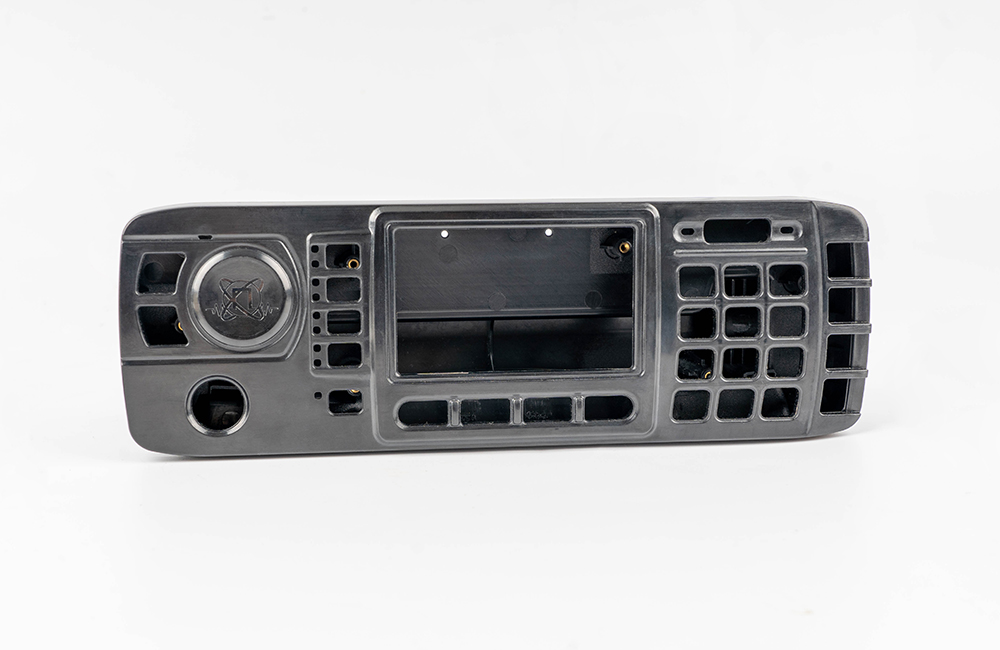
材料选择
ABS 塑料:具有良好的强度、韧性和表面光洁度,易于加工成型,能够满足遥控器外壳的基本性能需求,且成本相对较低。
PC 塑料:具有高透明度、高抗冲击强度和良好的耐热性,适用于需要高透明度或较高耐用性的遥控器外壳。
PP 塑料:具有比重轻、耐化学腐蚀性好、价格低廉等优点,常用于一些对成本敏感的普通遥控器外壳。
加工要点
材料预处理:在注塑前,确保塑料颗粒充分干燥,避免因含水率过高导致注塑过程中产生缺陷。
注塑工艺控制:合理控制注塑温度、压力和速度,确保每个遥控器零件的尺寸和性能符合要求。
模具维护:定期对模具进行清洁、润滑和保养,及时修复模具的磨损和损坏,以保证模具的使用寿命和注塑产品的质量。