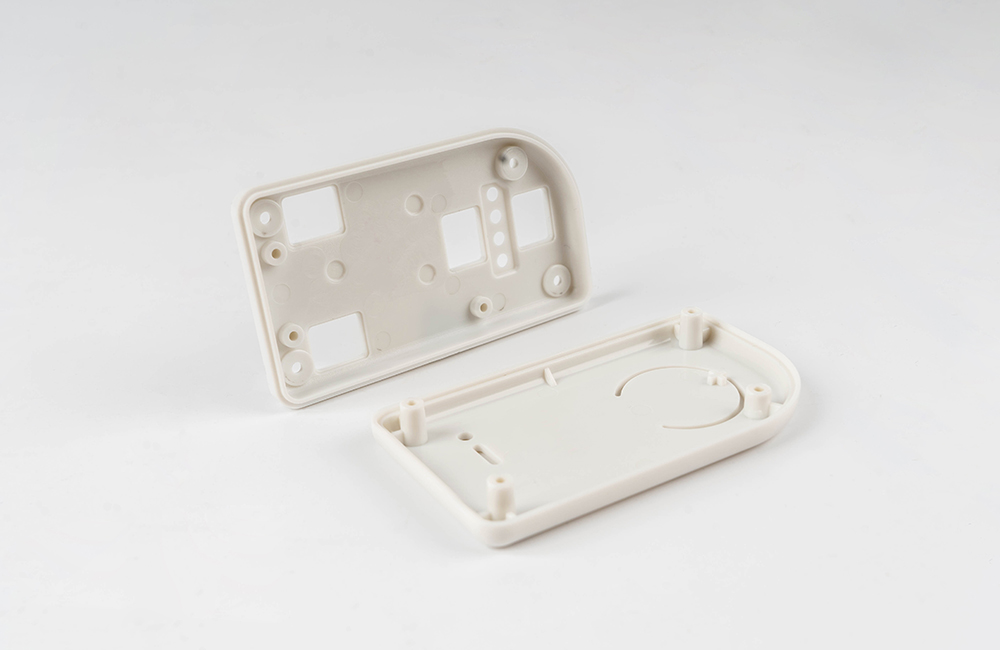
行业/分类:其他手板模型加工
加工方式: 注塑 使用材料: 塑料
最小精度: 0.1mm 生产周期: 2~7天
产品尺寸: 18cm*8cm*3cm
后处理: 喷油
制作流程
设计与建模
产品设计:根据小电子产品外壳的功能和外观需求,使用 CAD 等设计软件进行三维模型设计,确定外壳的尺寸、形状、结构等细节,如按键位置、接口形状、散热孔布局等。
模具设计:基于产品三维模型,设计注塑模具,包括确定分型面、浇口位置、冷却系统布局等,以确保在注塑过程中塑料熔体能够均匀填充型腔,且便于产品脱模。
材料选择
ABS 塑料:具有良好的机械性能、加工性能和表面光洁度,易于染色和涂装,适用于外观要求较高的小电子产品外壳,如手机外壳、相机外壳等。
PC 塑料:具有高强度、高透明度和良好的耐热性,常用于需要较高强度和透明度的外壳,如智能手表外壳、平板电脑外壳等。
PP 塑料:具有较好的耐腐蚀性、耐疲劳性和较低的密度,成本相对较低,适用于一些对成本敏感且要求一定性能的小电子产品外壳,如小型家电外壳等。
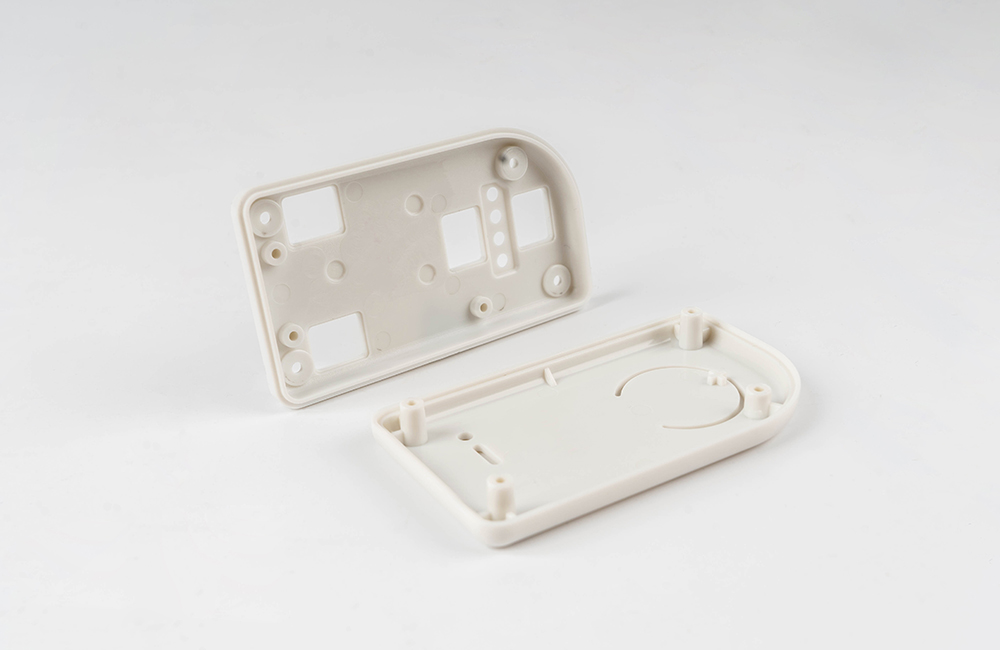
模具制作
CNC 加工:将设计好的模具模型数据导入 CNC 加工中心,通过铣削、钻孔等工艺对模具材料(如钢材)进行加工,制造出模具的型腔和型芯,加工精度可达到较高水平,能保证模具的尺寸精度和表面质量。
电火花加工:对于一些形状复杂、难以通过 CNC 直接加工的模具部位,可采用电火花加工方法,利用电火花放电产生的高温蚀除金属材料,精确地加工出模具的形状。
注塑成型
材料预处理:将所选的塑料颗粒进行干燥处理,去除水分和杂质,以防止在注塑过程中产生气泡、银丝等缺陷,影响产品质量,例如 ABS 塑料一般在 80℃-90℃的温度下干燥 4-6 小时。
注塑参数设置:根据塑料材料的特性、产品形状和模具结构,设置合适的注塑参数,包括注射压力、注射速度、保压压力、熔料温度、模具温度等,如对于薄壁结构的小电子产品外壳,需要较高的注射速度和压力,以确保熔体能够快速充满型腔。
注塑过程:将经过预处理的塑料原料加入注塑机的料筒中加热熔化,达到合适的黏度后,通过螺杆的推动作用将熔体注入模具型腔中,当塑胶熔体在模具型腔中冷却定型后,打开模具取出小电子产品外壳手板模型。
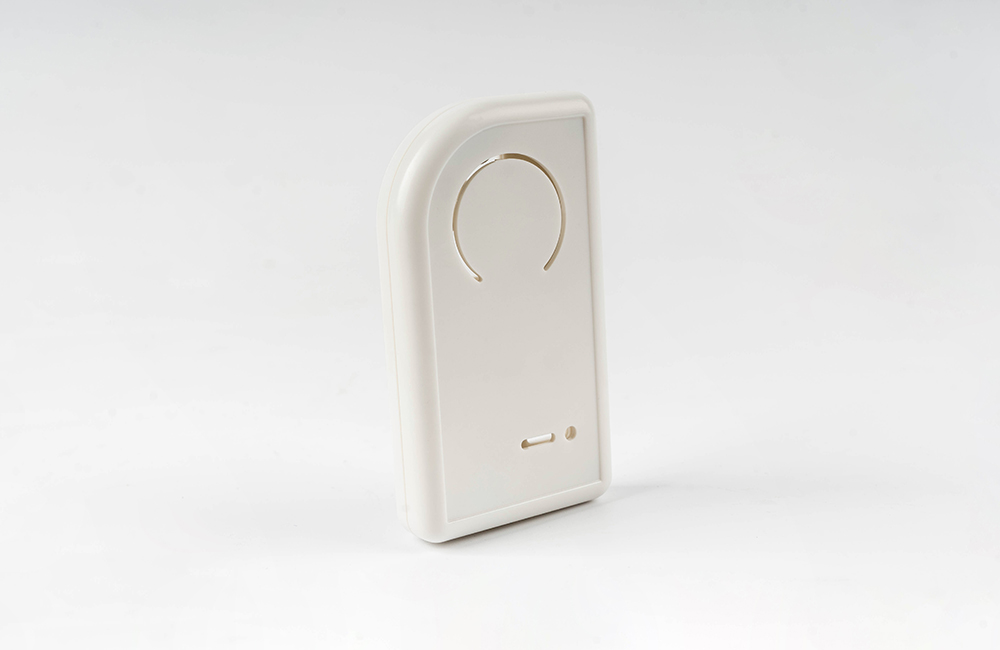
后处理
去毛刺与修剪:使用刀具、砂纸等工具去除产品边缘的毛刺、飞边和浇口残留,使产品外观更加整洁,尺寸符合设计要求。
表面处理:根据产品需求进行表面处理,如喷砂、抛光、喷漆、电镀等,以提高产品的外观质量、耐磨性和耐腐蚀性等,例如对手机外壳手板模型进行喷漆处理,可以获得不同的颜色和光泽效果。
装配与测试:将各个零部件进行装配,检查产品的装配精度和功能是否正常,如检查小电子产品外壳手板模型的按键是否能够正常按压、接口是否能够顺利连接等。
加工要点
精度控制:小电子产品外壳通常对尺寸精度要求较高,在模具设计和加工过程中,要严格控制尺寸公差,采用高精度的加工设备和测量仪器,确保产品尺寸符合设计要求,如手机屏幕边框的尺寸公差要求通常在 ±0.05mm 以内。
外观质量:外观质量直接影响小电子产品的市场竞争力,要注意模具表面的光洁度和加工工艺,避免在注塑过程中产生流痕、熔接痕、气纹等缺陷,同时要保证表面处理的质量,如颜色均匀性、附着力等。
脱模设计:为了便于产品从模具中顺利脱出,在模具设计时要合理设置脱模斜度和脱模机构,脱模斜度一般外表面取 0.5°-1°,内表面可以适当增加到 1°-3°,对于一些形状复杂的产品,还需要采用滑块、顶针等脱模机构。