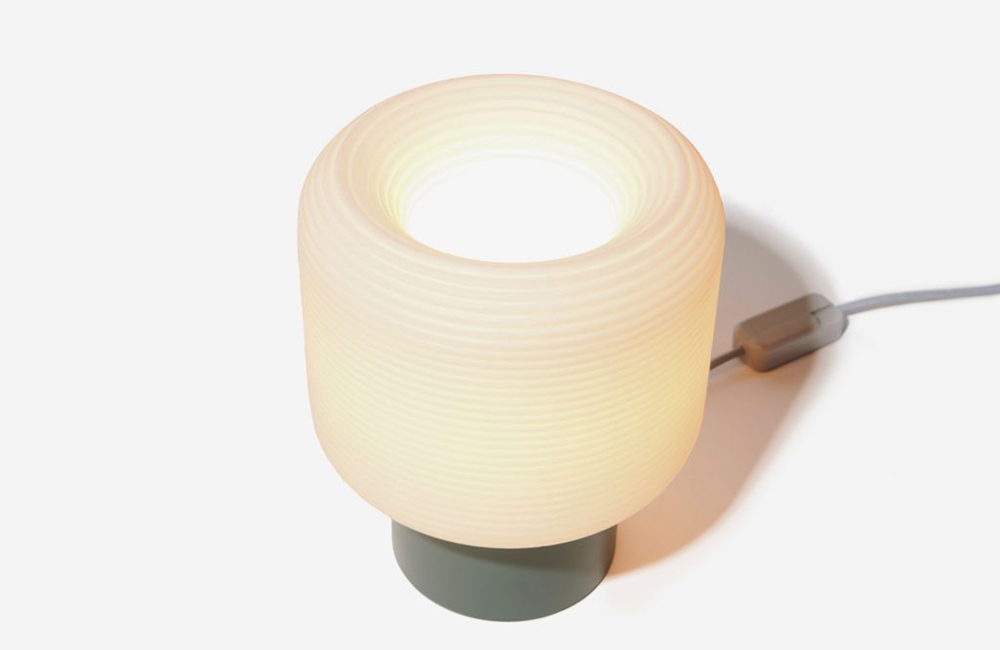
行业/分类:照明手板模型加工
加工方式: 3D打印 使用材料: 树脂
最小精度: 0.1mm 生产周期: 2~7天
产品尺寸: 18cm*18cm*16cm
后处理: 喷油
制作3D打印吊灯手板模型需要结合设计、3D建模、打印工艺和后处理等多个环节。以下是详细的流程指南,帮助你高效完成吊灯原型制作:
一、前期准备
明确需求
确定吊灯的设计用途(展示/功能测试/外观验证)。
确认尺寸、比例(建议按实际大小或缩放比例制作)。
规划结构细节(如透光部分、支撑骨架、安装配件等)。
工具与软件
3D建模软件:Blender(免费)、Fusion 360、Rhino、SolidWorks等。
切片软件:Cura、PrusaSlicer、IdeaMaker(根据打印机类型选择)。
打印机:FDM(熔融沉积)、SLA(光固化)、DLP(数字光处理)均可,需根据精度和材料需求选择。
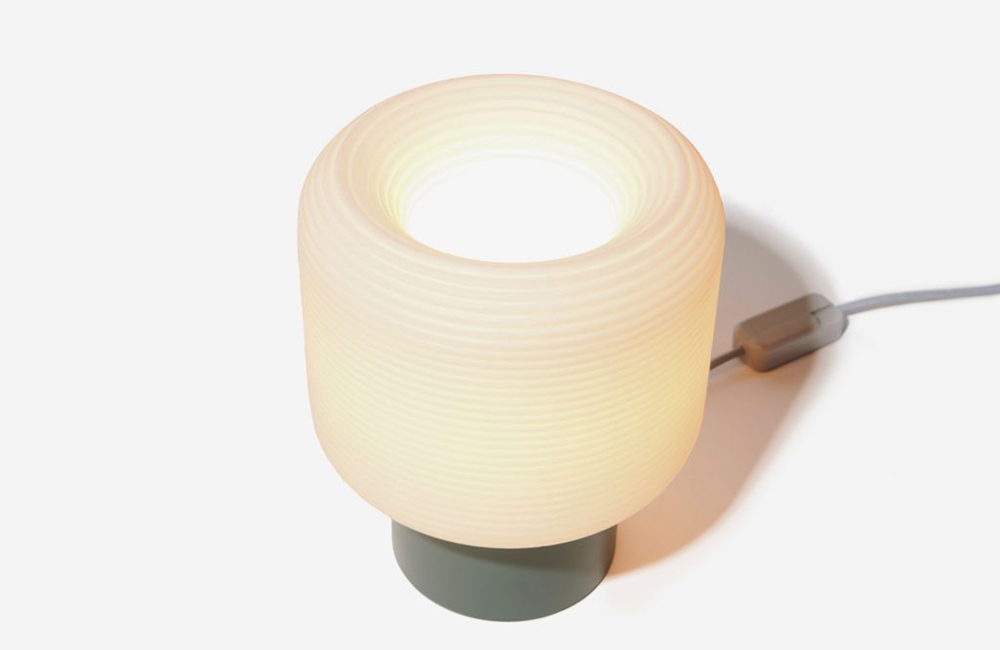
二、3D建模与设计优化
建模要点
结构设计:
悬垂部分需添加支撑结构(如柱体、框架),避免打印失败。
复杂曲面可拆分为多个部件(如灯罩、底座、支架),后期组装。
壁厚均匀:最小壁厚建议≥0.8mm(FDM)或≥0.5mm(光固化),避免打印变形。
透光设计:若需透光效果,使用半透明材料(如PETG、树脂),并设计蜂窝状或网格结构减少材料消耗。
支撑结构优化
使用软件自带的支撑生成功能(如Cura的“树形支撑”或“可溶支撑”)。
手动添加隐藏式支撑(如内部骨架),减少表面支撑痕迹。
文件检查
导出为.stl
或.obj
格式,检查是否有非流形边、重叠面等问题。
使用Meshmixer或Netfabb修复模型错误。
三、3D打印工艺选择
需求 | 推荐技术 | 材料 | 优势 |
---|---|---|---|
高精度细节 | SLA/DLP | 光敏树脂(半透明/白色) | 表面光滑,适合复杂曲面 |
大尺寸/低成本 | FDM | PLA、PETG、ABS | 材料经济,适合结构性部件 |
透光效果 | SLA/FDM | 半透明树脂/PETG | 光固化树脂透光性更佳 |
耐高温/机械强度 | SLS | 尼龙粉末 | 适合承重部件,但成本较高 |
四、打印参数设置
层高与速度
精细部件:层高0.1-0.2mm,打印速度40-60mm/s。
大尺寸结构:层高0.2-0.3mm,速度80-120mm/s(FDM)。
温度与冷却
PLA:喷嘴200-220℃,热床60℃。
ABS/PETG:喷嘴240-260℃,热床80-110℃,需密闭空间打印防翘曲。
开启风扇强制冷却,减少层纹。
支撑与填充
填充率:结构性部件20-30%,装饰性部件10%或蜂窝填充。
支撑角度:45-60°,便于手动拆除。
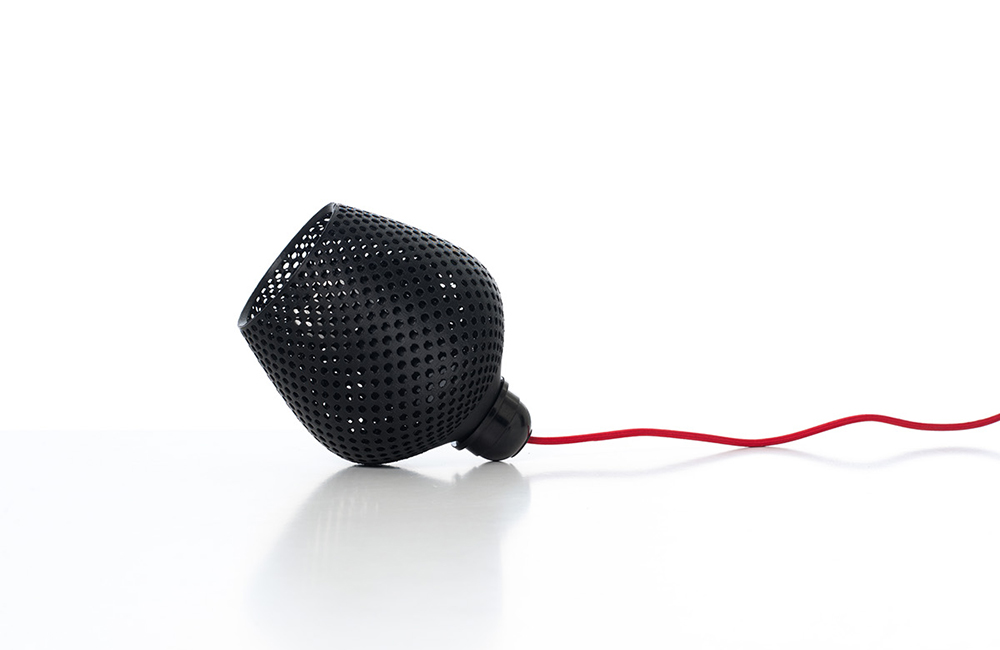
五、后处理工艺
去除支撑
用镊子或刀片小心拆除支撑,避免划伤表面。
可溶支撑(如HiPS)可浸泡于化学溶剂中溶解。
打磨与抛光
FDM打印件:用砂纸从粗到细(100→2000目)打磨层纹。
光固化件:酒精擦拭后抛光膏处理,达到镜面效果。
上色与涂层
喷涂哑光/亮光漆增强质感,或用水补土填补瑕疵。
透光部件可贴膜或喷涂半透明颜料。
组装与测试
使用胶水(如瞬干胶、环氧树脂)或螺丝固定部件。
测试悬挂稳定性,必要时添加配重或调整重心。
六、常见问题与解决方案
问题 | 原因 | 解决方法 |
---|---|---|
层裂或翘边 | 热床温度低/冷却过快 | 提高热床温度,减少风扇直吹 |
支撑难拆除 | 支撑角度过小/粘连严重 | 调整支撑角度,涂抹脱模剂(如PVA胶水) |
透光性差 | 材料不透明/表面粗糙 | 更换半透明材料,打磨至光滑 |
结构强度不足 | 填充率低/壁厚过薄 | 增加填充率或加厚关键部位 |
七、案例参考
极简几何吊灯:用FDM打印镂空几何框架,搭配亚克力片作为灯罩。
仿水晶吊灯:SLA打印透明树脂,模拟水晶折射效果,后期抛光处理。
模块化吊灯:拆分为多个可替换部件(如花瓣、立方体),支持自由组合。
通过以上步骤,你可以高效制作出兼具美观与功能的吊灯手板模型。如需进一步优化,建议结合实物测试反馈调整设计,或尝试不同材料与工艺的组合!