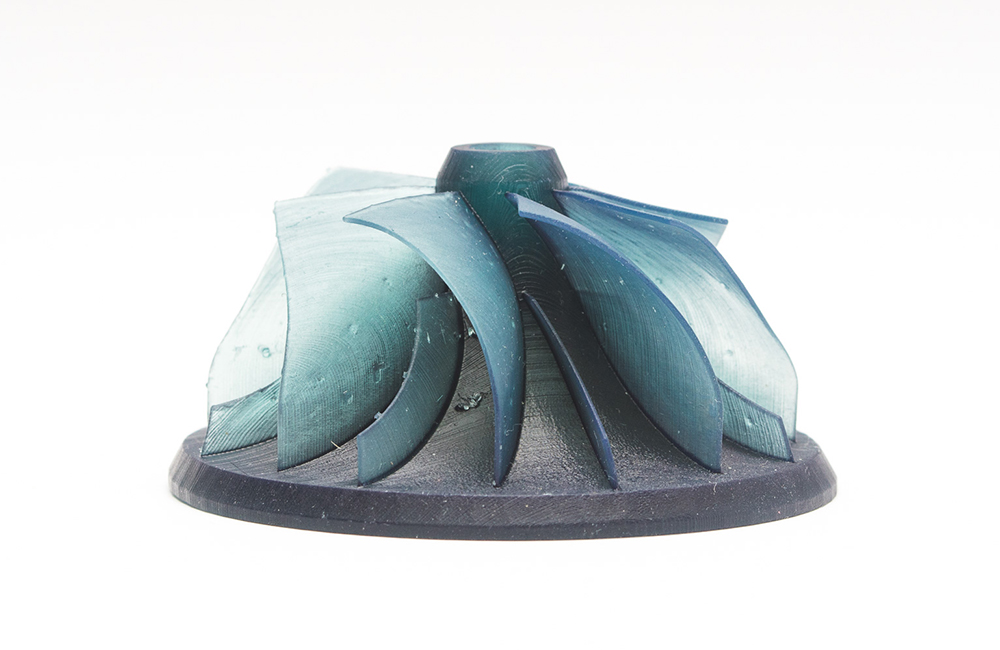
行业/分类:其他手板模型加工
加工方式: 3D打印 使用材料: 树脂
最小精度: 0.1mm 生产周期: 2~7天
产品尺寸: 8cm*8cm*4cm
后处理: 喷油
3D打印塑料涡轮手板模型是完全可行的,且具有成本低、速度快、设计自由度高的优势。以下是详细指南:
1. 3D打印塑料涡轮的适用场景
原型验证:测试涡轮结构、流体动力学性能或装配兼容性。
小批量生产:替代传统注塑,快速生产定制化涡轮。
教育/展示:用于教学演示或展览模型。
应急维修:快速制造替换零件。
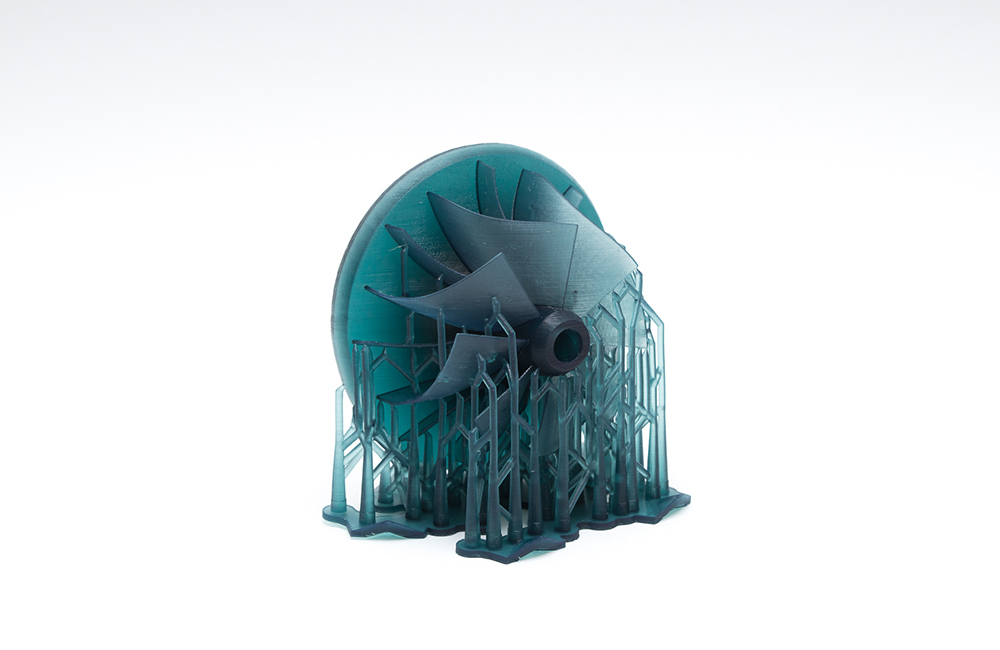
2. 可选3D打印技术及材料
(1)技术选择
技术 | 特点 | 适用材料 | 推荐场景 |
---|---|---|---|
FDM(熔融沉积) | 成本低、材料多样、适合中低精度需求 | PLA、ABS、PETG、TPU | 外观模型、功能验证 |
SLA(光固化) | 高精度、光滑表面、支持复杂结构 | 光敏树脂 | 精密模型、透明涡轮 |
SLS(粉末烧结) | 高强度、耐磨、支持全彩色 | 尼龙、TPU粉末 | 功能性零件、耐高温涡轮 |
Multijet 3D | 超高精度、类注塑效果 | 光敏树脂/蜡 | 高精度仿制、批量原型 |
(2)材料选择
PLA/ABS:
优点:低成本、易打印、机械性能适中。
缺点:耐温性差(PLA最高约60°C,ABS约100°C)。
适用:常温环境下的功能验证或展示模型。
PETG:
优点:耐温性更好(约80°C)、抗化学腐蚀。
适用:需要一定耐热性的涡轮(如汽车冷却系统)。
光敏树脂(SLA):
优点:高精度、表面光滑、可透明或半透明。
缺点:材料成本较高,需避光保存。
适用:精密流体动力学测试或透明涡轮模型。
尼龙(SLS):
优点:高强度、耐磨、耐温(约150°C)。
缺点:表面粗糙度较高,需后处理。
适用:功能性涡轮(如高温环境或长期使用)。
3. 设计注意事项
结构优化:
避免薄壁(建议壁厚≥0.5mm,根据打印技术调整)。
添加支撑结构(尤其是悬空部分或复杂曲面)。
优化叶片角度和厚度,确保流体效率。
公差控制:
FDM精度较低(±0.2mm),SLA/SLS精度较高(±0.1mm)。
关键尺寸需预留后处理余量(如打磨、抛光)。
装配兼容性:
如果涡轮需与其他部件配合,需考虑打印材料的收缩率(PLA约0.1%-0.2%)。
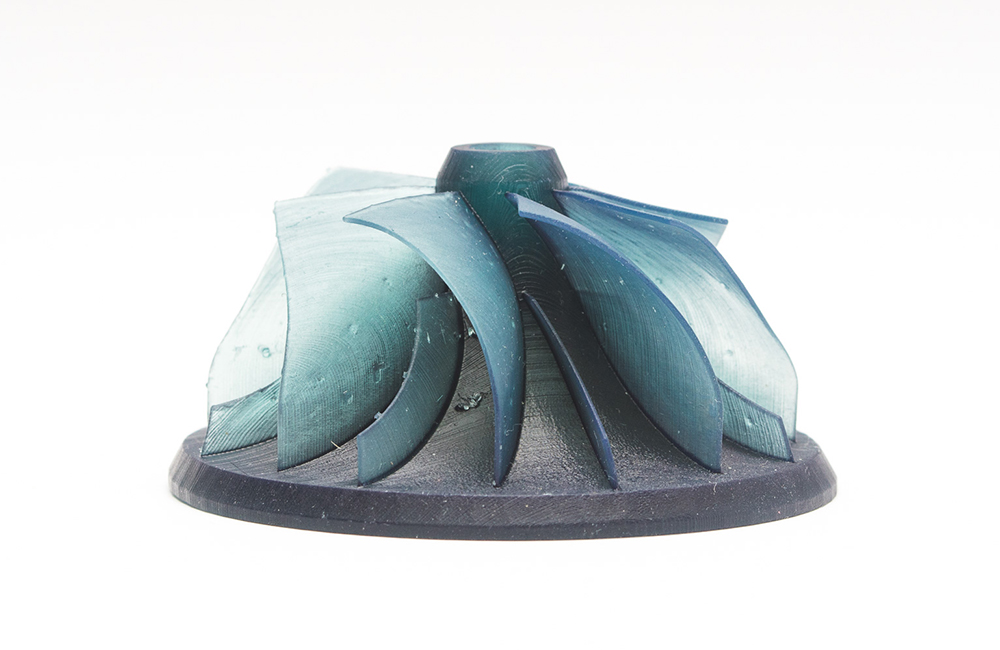
4. 打印与后处理步骤
(1)打印前准备
切片软件设置:
层厚:FDM建议0.2-0.3mm,SLA/SLS可低至0.05mm。
填充率:根据强度需求调整(通常20%-30%即可)。
支撑结构:对悬空叶片或内腔添加可剥离支撑。
模型方向:
将涡轮的轴线垂直于打印平台,减少支撑使用并提升表面质量。
(2)打印参数
技术 | 喷嘴温度 | 热床温度 | 打印速度 | 支撑间距 |
---|---|---|---|---|
FDM (PLA) | 190-210°C | 无(PLA冷床可贴附) | 30-50mm/s | 0.4-0.6mm |
SLA (树脂) | – | – | – | 自动生成 |
SLS (尼龙) | – | – | – | 自动生成 |
(3)后处理
去除支撑:用钳子或刀具小心拆除支撑结构。
打磨/抛光:
FDM模型:用砂纸打磨层纹,或使用丙酮蒸汽抛光(ABS)。
SLA模型:酒精清洗残留树脂,紫外二次固化。
SLS模型:喷砂处理表面粉末,或化学抛光。
染色/涂层:根据需求喷涂颜料或防水涂层(如聚氨酯涂料)。
5. 性能测试与优化
流体动力学测试:
通过风洞或水流量测试验证涡轮效率,优化叶片形状。
耐温/耐压测试:
在目标工作环境中测试涡轮的变形或损坏情况。
材料改性:
添加碳纤维增强PLA/ABS强度,或使用耐高温树脂(如聚醚醚酮PEEK)。
6. 替代方案(若3D打印不适用)
CNC加工:适合高精度、高强度金属涡轮,但成本高、速度慢。
硅胶复模:用3D打印母模制作硅胶模具,注塑生产批量塑料涡轮。
钣金/焊接:金属涡轮的传统工艺,适合工业级应用。
总结
3D打印塑料涡轮手板模型推荐使用FDM或SLA技术,材料可选PLA、ABS或光敏树脂,具体根据精度、耐温性和预算决定。设计时需优化结构并添加支撑,后处理包括打磨、抛光和涂层。若需功能性测试,可升级至SLS尼龙或高性能树脂。对于小批量或原型验证,3D打印是性价比最高的选择!