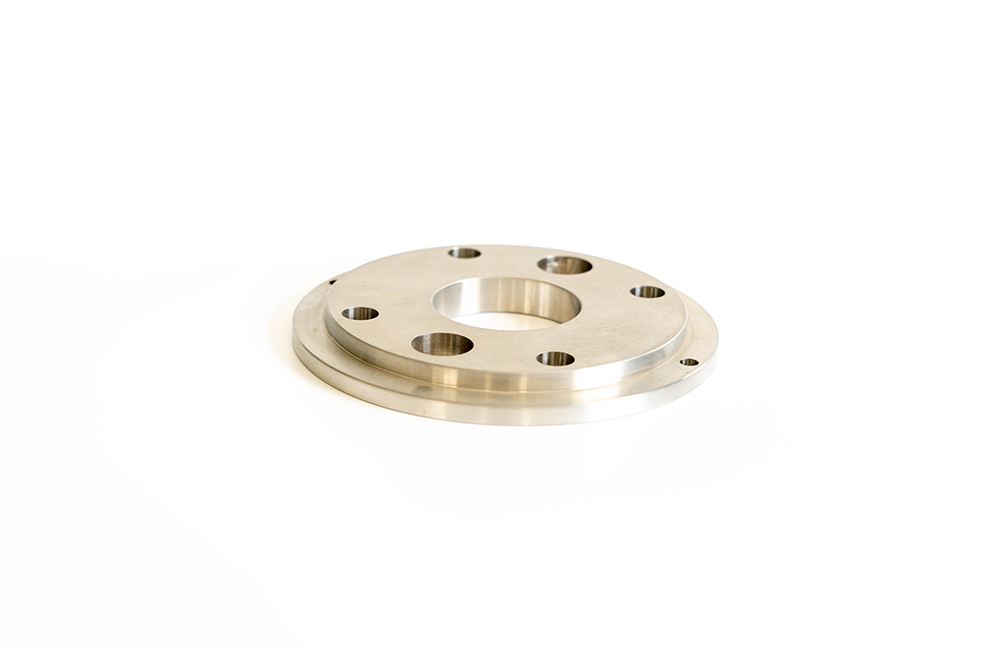
行业/分类:其他手板模型加工
加工方式: cnc加工 使用材料: 铝合金
最小精度: 0.05mm 生产周期: 2~7天
产品尺寸: 5cm*5cm*1cm
后处理: 打磨
一、前期准备
(一)材料选择
根据垫片的使用要求和性能特点,选用合适的金属材料,如不锈钢、铝合金等。确保材料表面无划痕、锈迹等缺陷,尺寸符合加工要求。
(二)设计图纸
使用专业的 CAD 软件绘制金属垫片的精确二维或三维图纸,标注清楚垫片的尺寸、公差、孔径、倒角等详细信息,为后续编程和加工提供准确依据。
(三)刀具与夹具准备
刀具:依据加工材料和图纸要求,选择合适的 CNC 刀具,如铣刀、钻头、镗刀等。对于金属加工,通常需要配备硬质合金刀具,以保证切削效率和刀具寿命。不同规格的刀具用于粗加工、半精加工和精加工阶段,例如粗加工可选用较大直径的铣刀快速去除余量,精加工则使用较小直径且精度高的刀具保证尺寸精度和表面质量。
夹具:根据垫片的形状和尺寸设计专用夹具,确保在加工过程中垫片能够被牢固地定位和夹紧,防止因切削力导致工件移位或变形。常见的夹具类型有平口钳、台钳、专用夹具等。对于批量较大的生产,专用夹具能够显著提高加工效率和一致性。
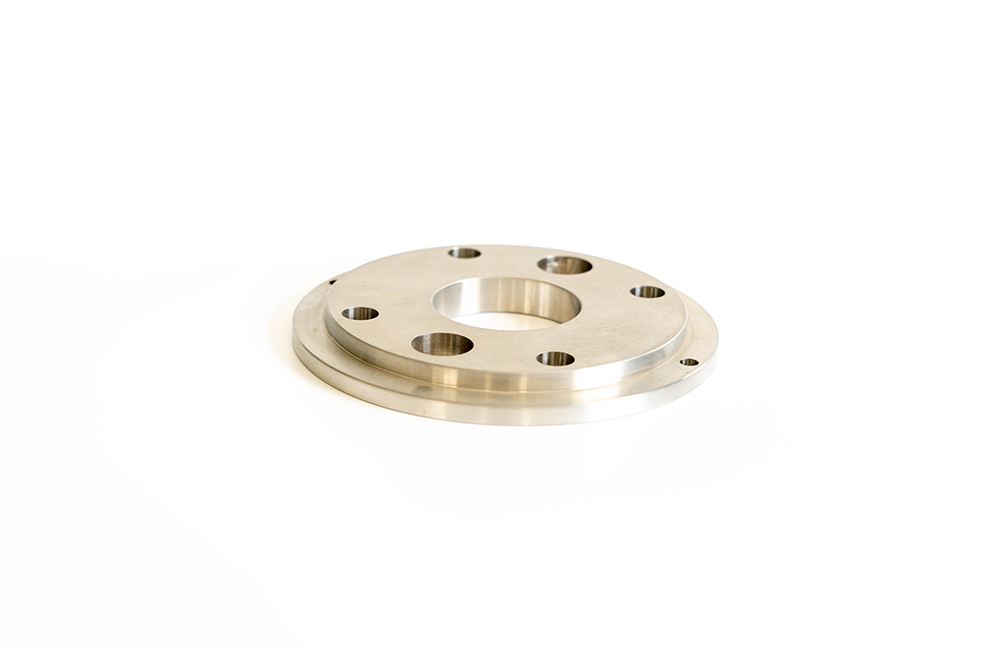
二、CNC 编程
(一)工艺分析
对金属垫片的加工工艺进行详细分析,确定加工顺序、切削参数等。一般先进行粗加工,去除大部分余量,然后进行半精加工和精加工,逐步提高尺寸精度和表面质量。例如,对于有孔的垫片,先加工外形轮廓,再进行钻孔、铰孔等操作;对于有螺纹的孔,还需安排攻丝工序。
(二)程序编制
使用专业的 CNC 编程软件(如 Mastercam、UG 等),根据设计图纸和工艺分析结果编制加工程序。设置好工件坐标系、刀具路径、切削速度、进给量、切削深度等参数。在编程过程中,要充分考虑刀具的切削轨迹,避免刀具与工件发生碰撞,同时优化切削路径,提高加工效率。例如,在铣削平面时,可采用行切法或环切法,根据垫片的形状和尺寸选择合适的切削方式;在钻孔时,要准确计算钻孔位置和深度,并设置合适的钻孔循环指令。
(三)程序验证
在实际加工前,通过软件的仿真功能对编写好的程序进行验证。检查刀具路径是否正确,是否存在过切、欠切、刀具碰撞等问题。如有错误,及时修改程序,直至仿真结果无误。
三、加工过程
(一)装夹工件
将金属垫片坯料正确安装在夹具上,使用百分表等工具找正工件的平行度、垂直度等,确保工件的装夹精度。调整夹具的夹紧力度,既要保证工件在加工过程中不会松动,又要避免因夹紧力过大导致工件变形。
(二)粗加工
按照编程设定的切削参数,启动 CNC 机床进行粗加工。粗加工时,主要目的是快速去除大量余量,使工件接近最终尺寸形状。在粗加工过程中,要注意观察切削状态,如切削力是否过大、刀具是否磨损、是否有异常振动等。如有异常情况,及时停机检查并调整切削参数或更换刀具。粗加工完成后,测量工件尺寸,检查余量是否均匀,如有不均匀情况,可在后续加工中进行调整。
(三)半精加工
在粗加工的基础上,进行半精加工。半精加工的目的是进一步提高尺寸精度和表面质量,为精加工做好准备。半精加工时,切削参数相对粗加工要小一些,刀具的切削刃应更加锋利,以保证加工表面的粗糙度。在加工过程中,要严格控制尺寸公差,对关键尺寸进行多次测量,确保尺寸精度符合要求。
(四)精加工
精加工是保证金属垫片尺寸精度和表面质量的关键步骤。使用高精度的刀具,按照精细的切削参数进行加工。在精加工过程中,要特别注意刀具的磨损情况,及时更换刀具,以保证加工精度的一致性。对于有较高表面质量要求的垫片,可采用镜面加工技术,使加工表面达到镜面效果。精加工完成后,再次测量工件尺寸,检查所有尺寸是否都在公差范围内,表面是否有划伤、凹坑等缺陷。
(五)孔加工与螺纹加工
如果金属垫片上有孔或螺纹,在完成外形加工后进行相应的孔加工和螺纹加工操作。钻孔时,要先使用中心钻打定心孔,然后再用钻头钻孔,以保证孔的位置精度。对于有精度要求的孔,可采用铰孔、镗孔等工艺进一步提高孔的尺寸精度和表面质量。螺纹加工时,根据螺纹规格选择合适的丝锥或攻丝刀具,设置正确的攻丝参数,如攻丝速度、进给量等,确保螺纹的精度和质量。
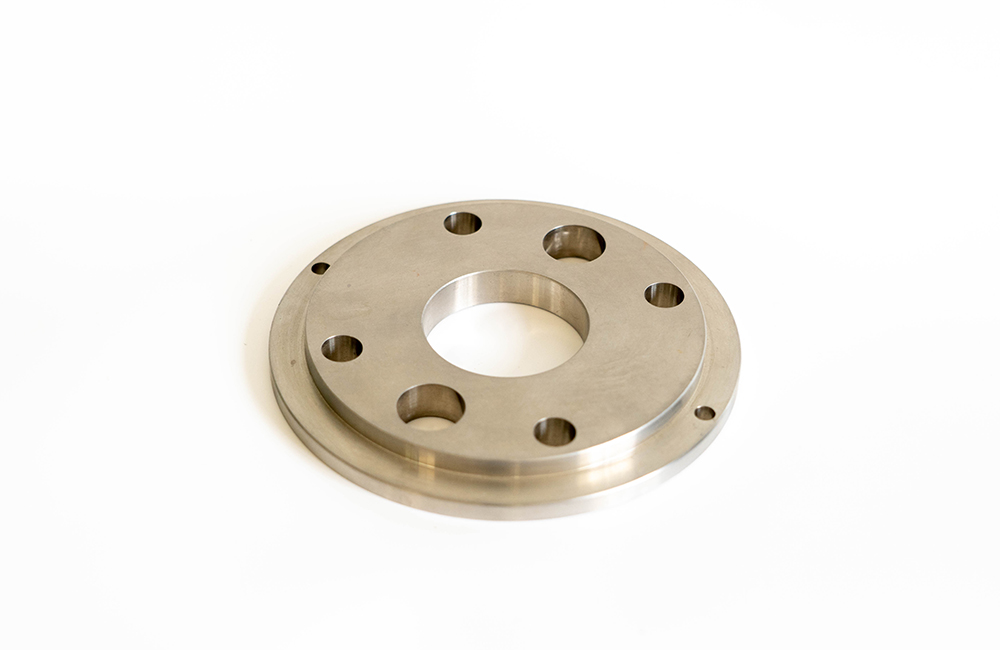
四、后处理
(一)去毛刺
金属垫片加工完成后,使用锉刀、砂纸等工具去除工件边缘和孔口的毛刺,防止毛刺影响装配和使用性能。对于一些难以去除的毛刺,可采用电解去毛刺、超声波去毛刺等工艺方法。
(二)清洗
将加工好的金属垫片放入清洗槽中,使用专用的金属清洗剂进行清洗,去除工件表面的油污、切削液残留等杂质。清洗后,用清水冲洗干净,并晾干或吹干。
(三)检测
使用卡尺、千分尺、三坐标测量仪等检测工具对金属垫片的尺寸、形状公差、位置公差等进行全面检测,确保垫片的各项参数符合设计要求。对于有特殊要求的垫片,如密封性要求较高的垫片,还需进行密封性测试,如采用气压试验、水压试验等方法检测垫片的密封性能。
(四)表面处理
根据金属垫片的使用环境和要求,对表面进行相应的处理。常见的表面处理方法有电镀、氧化、磷化等。例如,对于在潮湿环境中使用的不锈钢垫片,可进行钝化处理或镀铬处理,提高其耐腐蚀性;对于有装饰要求的铝合金垫片,可进行阳极氧化处理,获得不同颜色的氧化膜,增强美观性和耐磨性。
五、质量控制与检验标准
(一)尺寸精度
金属垫片的尺寸公差应控制在设计图纸规定的范围内,一般尺寸公差可参考 IT7 – IT9 级精度标准。例如,对于直径为 100mm 的圆垫片,其直径公差可控制在±0.05mm 以内。
(二)形状公差
垫片的平面度、圆度等形状公差应符合要求。平面度公差一般可控制在 0.02mm – 0.05mm 范围内,圆度公差可根据垫片的直径大小控制在相应范围内,如直径为 50mm 的圆垫片,圆度公差可控制在 0.03mm 以内。
(三)位置公差
孔与孔之间、孔与外轮廓之间的位置公差应满足装配和使用要求。例如,两个相邻孔的中心距公差可控制在±0.05mm 以内,孔与外轮廓的同轴度公差可控制在 0.03mm – 0.08mm 范围内,具体数值根据垫片的尺寸和精度要求确定。
(四)表面质量
加工表面应无明显的划伤、凹坑、锈迹等缺陷,表面粗糙度 Ra 值一般可控制在 0.8μm – 3.2μm 范围内,对于有较高表面质量要求的部位,如密封面,Ra 值可控制在 0.4μm – 0.8μm 范围内。
(五)硬度与力学性能
对于一些有特定力学性能要求的金属垫片,如弹簧垫片等,需检测其硬度和力学性能指标是否符合设计要求。硬度检测可采用洛氏硬度计、维氏硬度计等工具进行测量,力学性能测试可包括拉伸试验、压缩试验等,以检测垫片的抗拉强度、屈服强度、延伸率等指标。
通过以上详细的 CNC 加工金属垫片手板模型方案,可以制造出精度高、质量好的金属垫片手板模型,满足产品设计和研发的需求。在实际加工过程中,可根据具体情况对工艺参数和操作方法进行适当调整和优化,以确保加工效果和生产效率的最佳平衡。