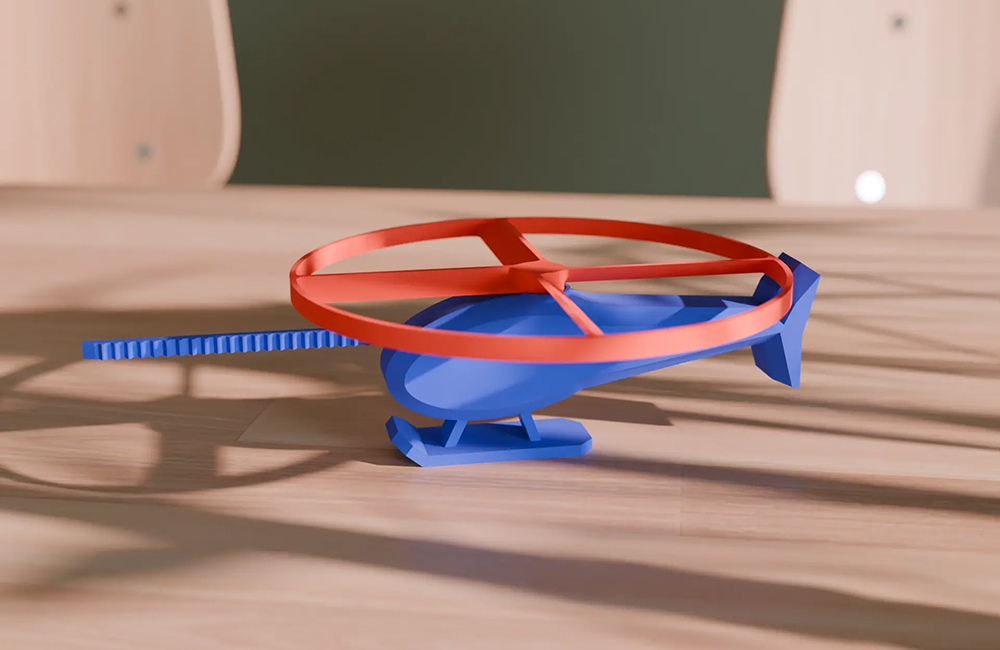
行业/分类:其他手板模型加工
加工方式: 3D打印 使用材料: 树脂
最小精度: 0.1mm 生产周期: 2~7天
产品尺寸: 18cm*14cm*10cm
后处理: 喷油
3D打印简易直升机玩具手板模型需兼顾外形还原、飞行功能与安全标准,通过轻量化设计和可动结构实现基础飞行演示。以下是从设计到成品的完整技术路径:
一、直升机结构解构与三维建模
核心部件参数化设计
机身框架:
尺寸:长 150mm× 宽 80mm× 高 60mm,壁厚 1.5mm(FDM)或 1mm(SLA);
轻量化:空心结构 + 十字支撑,重量≤30g(含电机)。
旋翼系统:
主旋翼直径 120mm,2 叶桨,桨距角 8°~12°;
尾旋翼直径 30mm,4 叶桨,与主旋翼转向相反。
动力系统:
预留电机仓:适配 N20 微型电机(直径 10mm,长 20mm);
电池仓:容纳 CR2032 纽扣电池(厚度 2mm),续航≥10 分钟。
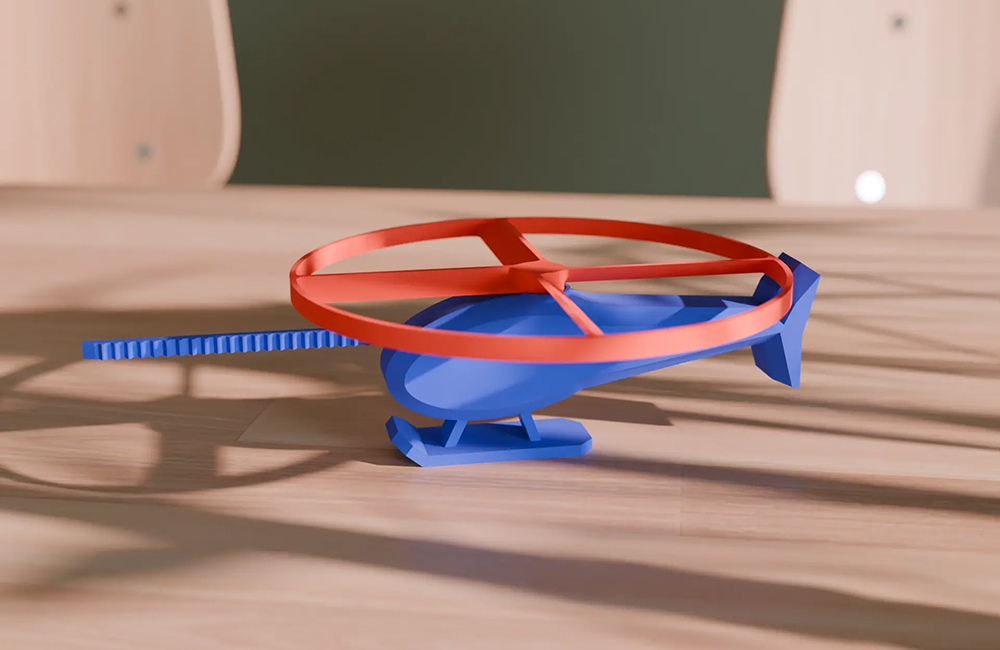
可动性建模要点
旋翼连接:
主旋翼轴孔直径 2mm,配合 1.8mm 不锈钢轴(间隙 0.2mm);
旋翼根部添加加强筋(厚度 1.5mm),防止旋转断裂。
起落架设计:
弹性材质:TPU 打印 C 型支架,减震行程 5mm;
离地间隙:15mm,避免着陆时机身触地。
二、打印工艺与材料选型
工艺类型 | 材料 | 适合部件 | 功能优势 |
---|---|---|---|
FDM(熔融沉积) | PLA/TPU | 机身、旋翼(成本低) | PLA 强度高,TPU 起落架减震性好 |
SLA(光固化) | 刚性树脂 | 细节部件(仪表盘、舱门) | 精度 ±0.05mm,表面光滑 |
多材料 3D 打印 | 刚性 + 柔性树脂 | 整体一次成型(硬软结合) | 旋翼刚性 + 起落架柔性同步实现 |
SLS(激光烧结) | 尼龙 12 | 耐磨损齿轮(传动系统) | 自润滑性好,寿命≥100 小时 |
材料组合案例:
机身:PLA(抗拉强度 40MPa),确保结构稳定;
旋翼:ABS(耐温性好,避免电机发热变形);
起落架:TPU 95A(邵氏硬度),断裂伸长率≥300%。
三、切片参数与打印优化
旋翼打印关键设置(FDM 工艺)
温度控制:
ABS 旋翼:喷头 240℃,热床 110℃,减少翘曲(变形量≤0.5mm);
支撑策略:
旋翼桨尖悬空部分采用 “线性支撑”,支撑角度 45°,接触点直径 1mm;
电机仓内部添加点状支撑,支撑直径 0.8mm,便于拆除。
多材料打印工艺(以 Stratasys J750 为例)
材料分布:
机身:VeroWhitePlus 刚性树脂;
起落架:TangoBlackPlus 柔性树脂(硬度 95A);
切片参数:
层厚 0.1mm,旋翼部分填充率 50%,提升抗扭强度。
四、后处理与功能集成
动力系统安装
电机固定:
机身电机仓预留 M2 螺丝孔,配合硅胶垫减震(噪音降低 5dB);
传动设计:
主旋翼通过 0.8mm 直径皮带传动,减速比 2:1(电机转速 10000rpm→旋翼 5000rpm)。
飞行性能优化
重心调整:
头部预埋 1g 铅块,确保重心位于机身前 1/3 处(偏移量≤2mm);
旋翼平衡:
动平衡测试:旋翼转速 3000rpm 时,振幅≤0.1mm,否则添加配重块(0.1g / 次)。
安全测试
跌落测试:1m 高度自由落体,机身无开裂(安全系数≥1.5);
旋转安全:旋翼防护罩强度测试,施加 5N 径向力不断裂。
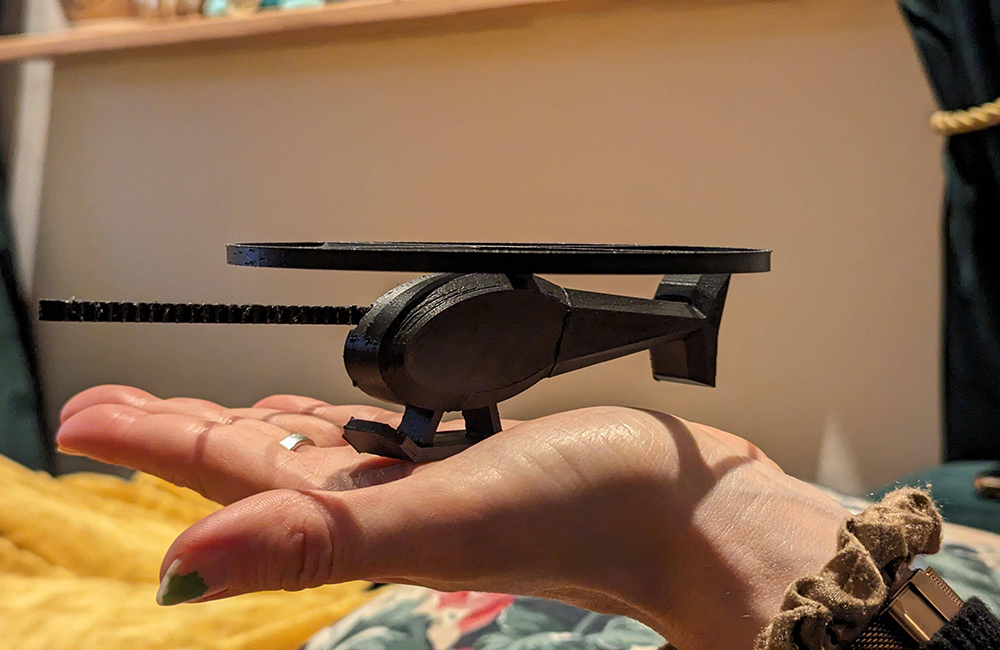
五、设计避坑与成本控制
结构禁忌
旋翼桨叶厚度≥1.5mm,避免高速旋转时断裂;
电机仓与机身连接宽度≥5mm,防止振动脱落。
低成本方案
部件拆分打印:
机身、旋翼、起落架分件打印,组装时用 AB 胶固定;
省略尾旋翼,改为固定导流片,降低结构复杂度(成本降低 30%)。
模块化设计
旋翼轴孔通用化:适配不同直径电机轴(1.5-2mm),便于升级;
电池仓预留扩展空间,可升级为可充电锂电池(3.7V,50mAh)。
六、应用场景与创新案例
科教教具:
SLA 打印透明树脂机身,内部展示传动结构,旋翼标注空气动力学参数;
配套 APP 显示实时转速、电池电量,用于物理课程演示。
儿童玩具:
FDM 打印彩色 PLA 直升机,旋翼边缘添加荧光条(波长 450nm),夜间飞行可见;
材料通过 EN71 认证,所有锐边倒圆角(R≥2mm)。
微型无人机原型:
尼龙打印机身,集成微型飞控板(尺寸 15×15mm),实现简单悬停功能;
旋翼采用快拆设计,便于运输更换(拆装时间≤1 分钟)。
七、安全标准与合规
儿童玩具安全:
旋转部件防护罩间隙≤3mm(防止夹伤手指);
小部件(如螺丝)拉力≥90N,避免误吞。
电磁兼容性:
电机驱动电路需通过 FCC 认证,辐射干扰≤40dBμV/m(30-1000MHz)。
通过 3D 打印技术,简易直升机玩具手板模型可快速实现从概念设计到功能验证的迭代,尤其适合教育玩具、微型飞行器原型开发,相比传统注塑工艺缩短 60% 的开发周期。