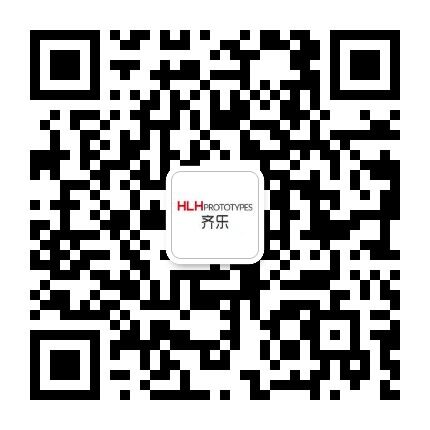
微信客服

在线客服
工业3d打印怎么打精细
发布时间:2025年03月24日
在工业3D打印中,要实现精细打印,需要从多个方面进行考虑和优化。以下是一些关键的方法:
高精度设备选型
选择合适的3D打印机:不同品牌和型号的工业3D打印机在精度上存在差异。例如,一些采用激光粉末烧结(SLS)技术的工业级3D打印机,如EOS LP – S 400,能够实现较高的成型精度,其打印层的厚度可以精确控制到较小尺寸,通常层厚可达到0.05 – 0.1mm左右。而立体光固化(SLA)技术的3D打印机,如Formlabs Form 3,通过使用高精度的激光光源和精密的光路系统,能够实现更小的层厚,一般在0.025 – 0.1mm之间,能打印出表面更加光滑、细节更加丰富的零件。
考虑设备的分辨率:设备的横向和纵向分辨率对打印精度有重要影响。以数字光处理(DLP)技术的3D打印机为例,其投影仪的分辨率决定了打印零件在平面方向上的精细程度。较高分辨率的投影仪,如4K甚至更高分辨率的设备,能够投射出更清晰的图像,从而打印出具有更精细细节的零件。
设备校准
平台校准:确保打印平台的平整度至关重要。在打印前,需要使用专业的工具(如激光水平仪)对平台进行校准。如果平台存在倾斜或不平整的情况,会导致打印的每一层厚度不一致,影响最终零件的尺寸精度和表面质量。例如,在FDM(熔丝沉积成型)技术中,第一层的高度校准尤为关键,它直接影响后续每一层的沉积情况。
喷头/激光器校准:对于FDM打印机,喷头的吐丝位置和速度需要精确校准。喷头应在合适的高度和角度下吐丝,以确保丝材均匀地沉积在平台上。对于基于激光的3D打印技术(如SLS、SLA),激光器的聚焦和功率分布需要调整到最佳状态。例如,在SLA打印中,激光焦点的位置如果不正确,会导致打印的模型出现模糊的边缘或者曝光过度/不足的情况。
高性能材料选用
选择合适的材料类型:不同的材料具有不同的特性,对打印精度的影响也不同。例如,对于需要高精度打印的精细零件,如精密模具或医疗器械零部件,通常会选择具有低膨胀系数和高流动性的光敏树脂(用于SLA)、金属粉末(用于SLS)等材料。光敏树脂在固化过程中体积收缩率小,能够保证打印零件的尺寸精度;细粒径的金属粉末则可以提供更细腻的表面质量和更高的成型精度。
材料的粒度和纯度:材料的粒度越小,越有利于打印出精细的细节。例如,在金属3D打印中,使用气雾化金属粉末比水雾化粉末具有更细的粒度和更好的流动性,能够打印出表面粗糙度更低、精度更高的零件。同时,材料的纯度也会影响打印质量,高纯度的材料可以减少杂质对打印过程的干扰,提高零件的物理性能和外观质量。
材料预处理
干燥处理:对于受潮的材料,如某些光敏树脂和金属粉末,在使用前需要进行干燥处理。受潮的材料可能会导致打印过程中出现气泡、强度降低等问题。例如,光敏树脂如果含有水分,在紫外光固化过程中会产生气泡,影响打印零件的密度和力学性能。可以通过加热干燥或真空干燥的方式对材料进行处理,确保材料的含水率在合适的范围内。
混合与搅拌:对于一些复合材料或多种成分混合的材料,充分的混合和搅拌是保证打印质量的关键。例如,在陶瓷3D打印中,陶瓷粉末和有机粘结剂需要均匀混合,否则会导致打印出的零件成分不均匀,出现开裂、变形等问题。可以使用机械搅拌器或球磨机等设备对材料进行混合,确保各成分分布均匀。
层厚设置
合理选择层厚:层厚是影响打印精度的关键因素之一。较小的层厚可以打印出更精细的细节,但同时也会增加打印时间和成本。在保证打印质量的前提下,需要根据实际情况选择合适的层厚。例如,对于具有复杂几何形状和精细结构的零件,可以将层厚设置为0.05 – 0.1mm;对于一些对强度要求较高、形状相对简单的零件,可以适当增加层厚至0.2 – 0.3mm。
自适应层厚技术:有些先进的3D打印机支持自适应层厚功能。打印机可以根据模型的不同部分自动调整层厚,在需要精细表现的区域使用较小的层厚,在平坦或不重要的区域使用较大的层厚。这样可以在保证打印质量的同时,提高打印效率。
打印速度与加速度
控制打印速度:打印速度过快可能会导致打印质量下降,出现层与层之间的粘连、丝材断裂(FDM)或树脂固化不充分(SLA)等问题。在不同的打印阶段和不同的材料下,需要调整打印速度。例如,在FDM打印中,打印外轮廓时速度可以适当放慢,以保证轮廓的清晰度;在填充内部区域时,可以加快速度。一般来说,对于精细零件的打印,速度应控制在较低水平,如10 – 30mm/s。
调整加速度:加速度的合理设置可以避免打印过程中的惯性力导致零件变形或损坏。特别是在启停阶段和方向改变阶段,加速度不宜过大。对于高精度的3D打印,加速度可以设置在较低值,如5 – 10mm/s²,以确保打印过程的稳定性。
温度控制
加热床温度(针对FDM等技术):合适的加热床温度有助于提高第一层与平台的附着力,减少零件的翘曲变形。不同的材料需要不同的加热床温度,例如,对于PLA材料,加热床温度一般在60 – 70°C;对于ABS材料,加热床温度通常在90 – 110°C。准确的加热床温度可以使第一层均匀地铺在平台上,为后续的打印提供良好的基础。
打印头温度(针对FDM等技术):打印头温度需要根据材料的类型和特性进行调整。合适的温度可以确保丝材顺利熔化并挤出,同时避免温度过高导致丝材碳化或过低导致丝材堵塞。例如,对于聚碳酸酯(PC)材料,打印头温度可能需要达到260 – 280°C才能正常打印。
环境温度控制:在一些对温度敏感的材料(如光敏树脂)的打印过程中,环境温度的控制也很重要。温度变化可能会导致材料的性能发生变化,影响打印精度。可以通过安装空调或恒温设备来保持打印环境的温度稳定,一般将环境温度控制在20 – 25°C之间。
切片精度设置
高精度切片算法:选择具有高精度切片算法的切片软件。例如,一些先进的切片软件(如Simplify3D、PrusaSlicer等)提供了高质量的六面体网格划分和自适应切片功能。这种算法能够更准确地将3D模型转换为打印路径,减少因切片导致的模型失真。在切片过程中,软件会根据模型的几何形状自动调整切片的方向和位置,以提高切片的精度。
切片厚度调整:除了在打印机上设置层厚外,在切片软件中也可以对切片厚度进行微调。有些切片软件允许用户根据模型的不同部分设置不同的切片厚度,例如,在模型的薄壁部分可以设置更薄的切片厚度,以保证足够的支撑强度;在模型的厚实部分可以适当增加切片厚度,提高打印效率。
支撑结构优化
自动生成支撑:对于具有悬垂结构的模型,需要添加支撑结构来保证打印过程中的稳定性。切片软件可以根据模型的形状自动生成支撑结构。在设置支撑时,需要考虑支撑的角度、密度和易去除性。一般来说,支撑的角度应与打印平台呈45° – 60°夹角,这样既可以提供足够的支撑力,又便于后处理时去除支撑。
手动调整支撑:自动生成的支撑结构可能并不完全符合实际需求,用户可以手动对支撑进行编辑和优化。例如,在支撑与模型接触的部位添加一些小的支撑点或加强筋,以提高支撑的稳定性;在不影响打印质量的前提下,尽量减少支撑的使用量,以降低后处理的难度。
去除支撑与毛刺处理
机械去除:对于FDM打印的零件,去除支撑后可能会留下一些毛刺和飞边。可以使用小型的工具(如镊子、刀片、砂纸等)小心地去除这些多余的部分。在去除过程中,要注意不要损坏零件的表面。例如,对于精细的塑料零件,可以使用锋利的刀片沿着支撑与零件的连接处轻轻地切割,然后使用砂纸打磨平整。
化学腐蚀去除(针对特定材料):对于一些金属材料或特殊塑料材料,可以采用化学腐蚀的方法去除支撑和毛刺。例如,对于铝合金零件,可以使用稀盐酸溶液浸泡一段时间,使支撑部分溶解掉。但这种方法需要严格控制腐蚀的时间和浓度,以免对零件本身造成腐蚀损伤。
表面处理
打磨与抛光:打磨和抛光是提高打印零件表面质量的常用方法。可以使用不同粒度的砂纸(从粗到细)对零件表面进行打磨,去除表面的层纹和不平整部分。例如,对于SLA打印的光敏树脂零件,先使用较粗(如200目)的砂纸打磨去除大的瑕疵,然后逐渐使用更细(如1000目以上)的砂纸进行精磨,最后使用抛光膏和抛光轮进行抛光处理,使零件表面达到镜面效果。
涂层处理:根据零件的应用需求,可以在表面涂上一层特殊的涂层来提高其性能和外观质量。例如,对于金属零件,可以涂上一层防锈漆或耐磨涂层;对于塑料零件,可以涂上一层水性清漆或UV固化涂层。涂层处理不仅可以改善零件的表面光洁度,还可以增加零件的耐磨性、耐腐蚀性等功能。
上一篇: 模型制作怎么做
下一篇: 3d打印是怎么打印的